An Overview of ISO 5 Cleanroom - Class 100 Cleanroom
In our previous articles, we have explored the cleanroom standards of Class 100,000, 10,000, and 1,000, which represent cleanrooms ranging from low to moderate cleanliness levels. So, what about a Class 100 cleanroom?
- What is an ISO 5 Cleanroom (Class 100 Cleanroom)?
- ISO 5 Cleanroom - Class 100 Cleanroom Standard
- Specifications for Designing an ISO 5 Cleanroom
- Essential Equipment for an ISO 5 Cleanroom
- Proposal for Gowning Room in ISO 5 Cleanroom
- Requirements for Inspection and Maintenance of ISO 5 Cleanroom (Class 100 Cleanroom)
And in this article, Vietnam Cleanroom will delve into an ultra-clean environment, the ISO 5 cleanroom (also referred to as Class 100 cleanroom). Let's explore the specific requirements for this type of cleanroom.
What is an ISO 5 Cleanroom (Class 100 Cleanroom)?
A Class 100 cleanroom is a highly controlled environment with stringent cleanliness requirements, maintaining air cleanliness levels at a maximum of 100 particles larger than 0.5 µm per cubic foot of air within the room.
According to the ISO 14644-1 standard, it is designated as an ISO 5 cleanroom, where the air is maintained at fewer than 3,520 particles > 0.5 µm per cubic meter of air in the room.
Common applications for Class 100 cleanrooms (ISO 5 cleanrooms) include the production of semiconductors and pharmaceutical compounding rooms.
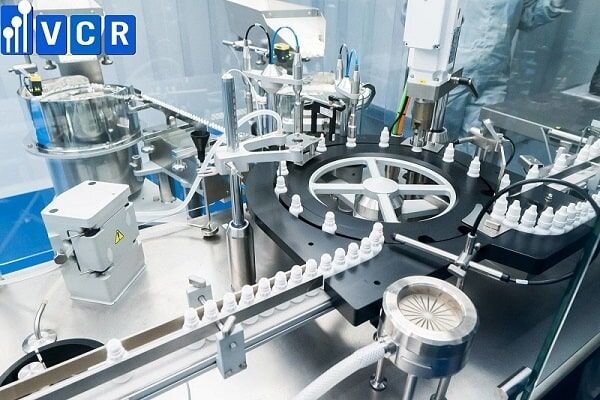
ISO 5 Cleanroom - Class 100 Cleanroom Standard
In the classification of cleanrooms based on the maximum allowable particle concentration per unit volume of air (cubic meter per ISO, cubic foot per STD 209E), the higher the particle concentration, the lower the cleanliness level. Therefore, when classifying cleanrooms from ISO 1 to ISO 9, cleanliness decreases as you move further back (ISO 1 being the cleanest, and ISO 9 being the least clean).

As it is known, an ISO 5 cleanroom is equivalent to a Class 100 cleanroom according to the STD 209E standard. Let's explore its allowable particle levels according to these two standards:
ISO 5 Cleanroom Standard per ISO 14644-1
We also understand that ISO 14644-1 replaced the STD 209E standard in 2011 and represents particle allowances per cubic meter. For ISO 5 cleanrooms, it specifies as follows:
Size |
≥0.1 µm |
≥0.2 µm |
≥0.3 µm |
≥0.5 µm |
≥1 µm |
≥5 µm |
Particle count |
100.000 |
23.700 |
10.200 |
3520 |
832 |
293 |
Class 100 Cleanroom Standard per STD 209E
Although it has been replaced by the ISO standard, STD 209E is still used for calculations and reference purposes. This standard governs cleanrooms by representing particle counts per cubic foot of air. For Class 100 cleanrooms, it is specified as follows:
Size |
≥0.1 µm |
≥0.2 µm |
≥0.3 µm |
≥0.5 µm |
≥1 µm |
≥5 µm |
Particle count |
750 |
300 |
100 |
Specifications for Designing an ISO 5 Cleanroom
Filtering and Particle Control
- Focus on controlling particles larger than 0.5 µm and smaller than 5 µm
- HEPA filter efficiency: 99.99% at 0.3 µm
- The end of the filtration process typically uses either a Hepa Box or an FFU (Fan Filter Unit), depending on the cleanroom's application.
- Particle count of less than 35,200 particles at the 0.5 µm size
- Other parameters such as temperature, humidity, lighting, noise, and exhaust control will be specifically required based on the cleanroom design.
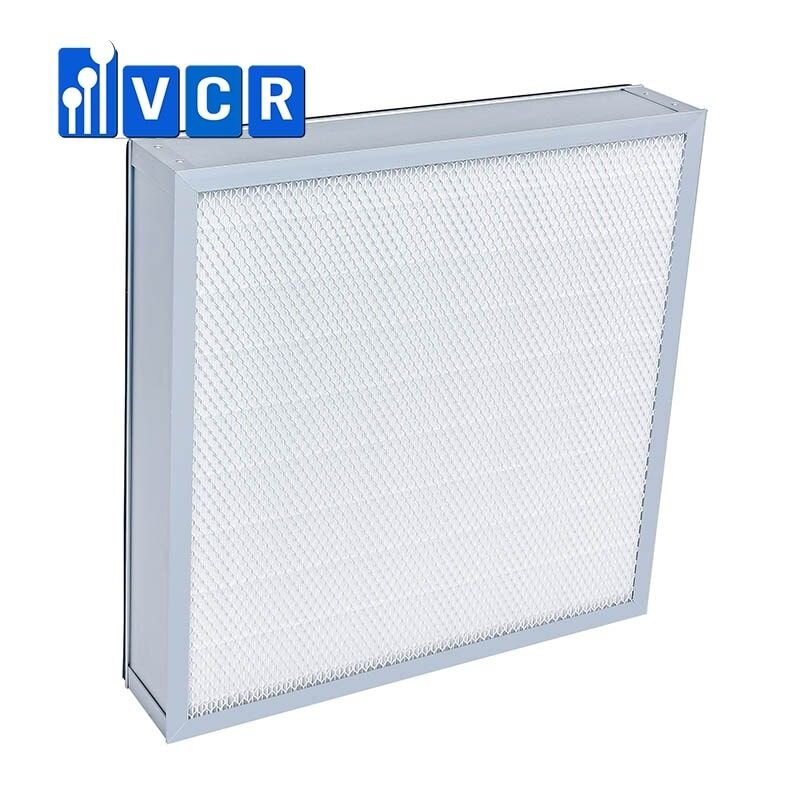
Airflow and Air Exchange Rates
- Due to the stringent cleanliness requirements of an ISO 5 cleanroom, the airflow is typically designed to be unidirectional (laminar flow). Laminar flow involves a vertical downward airflow that returns through the air handling system via return vents.
- Air Changes per Hour (ACH) in the cleanroom: 240 - 480 exchanges per hour
- Filter coverage efficiency: 60 - 70%
Architectural Features and Finishes:
- Wall Structure: The wall structure is constructed modularly, depending on the cleanroom's application. Biotechnology applications require a non-changeable system with smooth connections and rounded corners to eliminate 90° angles, allowing for wet cleaning or VHP misting to meet aseptic requirements. Nano-technology and other non-aseptic cleanroom applications typically use systems that are regularly wiped clean or dusted.
- Ceiling Structure: The ceiling structure is built purposefully for ISO 5 conditions, depending on the cleanroom's application. Biotechnology and pharmaceutical applications often require a standard modular ceiling system to achieve adequate filter coverage and appropriate lighting levels. Nano-technology and other non-aseptic applications often use sealed grid systems with empty ceiling tiles where there are no fixtures like filters or lighting, or they use complete modules.
- Flooring Systems include vinyl flooring, raised flooring, epoxy coatings, etc. Each system can provide specific attributes based on the application (e.g., chemical resistance, coving, static control, load-bearing/impact resistance, anti-slip properties).
- Other architectural features include various types of entry doors, observation windows, glass partitions, pass-throughs, water spray/fire alarm heads, Wi-Fi/network access, security cameras, and access control devices.
- Air Return: Low walls or raised floors.
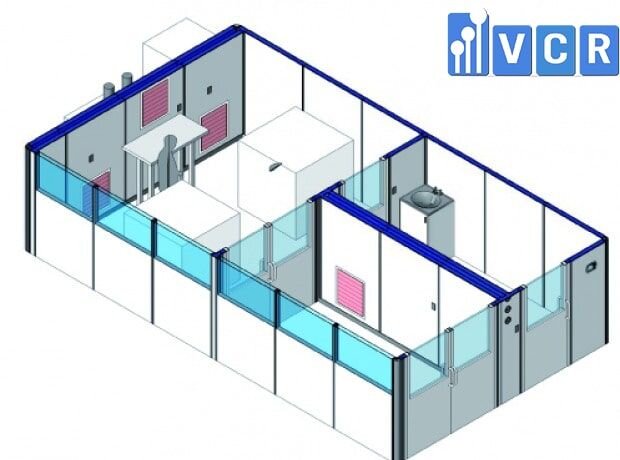
Essential Equipment for an ISO 5 Cleanroom
A Class 100 cleanroom demands an extremely high level of cleanliness, and as such, it requires a variety of equipment and accessories to meet these cleanliness standards. The specific equipment may vary depending on the cleanroom's application, but here are some typical requirements for equipment in an ISO 5 cleanroom:
- Pass Box
- Air Shower
- FFU - Fan Filter Unit
- Air Lock Room
- Cleanroom Gowning
- AHU System (Air Handling Unit)
- Tacky Mats
- Vinyl Flooring or Self-Leveling Epoxy Flooring
- Cleanroom Lighting
- Material Requirements for the Cleanroom
- Stainless Steel Furnishings
Proposal for Gowning Room in ISO 5 Cleanroom
Recommended Clothing Requirements:
- Head covering (hood or cap)
- Safety goggles or face shield
- Beard cover
- Laboratory coat or gown
- Shoe covers or high-top shoes
- Appropriate gloves for the task (e.g., vinyl, rubber, nitrile)
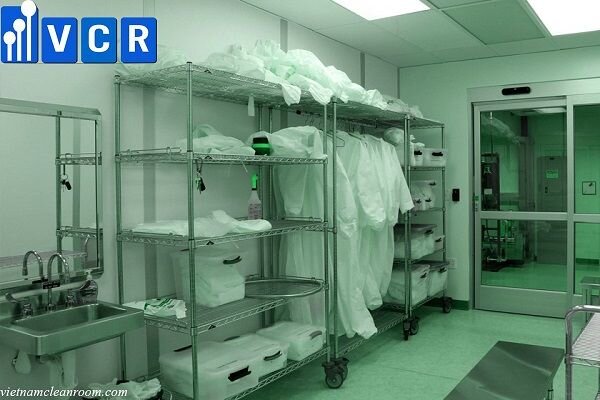
Requirements for Inspection and Maintenance of ISO 5 Cleanroom (Class 100 Cleanroom)
- Particle Count Inspection: Maximum interval of 6 months, following ISO 14644-1 testing procedure in Appendix A.
- Pressure Differential Inspection: Maximum interval of 6 months, following ISO 14644-1 testing procedure in Appendix B5.
- Airflow Rate Inspection: Maximum interval of 6 months, following ISO 14644-1 testing procedure in Appendix B4.
A Class 100 cleanroom is an environment with extremely high cleanliness requirements. Creating such an environment necessitates significant investment and demands meticulous design and construction.
PN