Cleanroom Gowning – Procedure Step By Step And Everything You Need To Know
In cleanrooms, the adoption of proper gowning practices plays a pivotal role in combatting the ever-present challenge of contamination.
The tiniest particles carried by human presence, imperceptible to the naked eye, can jeopardize cleanroom integrity. This article delves into essential gowning procedures, emphasizing the significance of adhering to meticulous protocols. Additionally, we also explore the crucial role of cleanroom gowning equipment in maintaining a controlled and sterile environment. And now let's find out with VCR.
Why use Cleanroom Gowning
The adoption of Cleanroom Gowning practices represents an indispensable measure in combating the prevalent challenge of cleanroom contamination. The human presence, though imperceptible to the naked eye, bears billions of minuscule particles, readily dispelled from the epidermis, hair, or garments. Unwittingly donning unsuitable attire or omitting crucial steps in the meticulous garbing procedure can expeditiously engender contaminated workspaces, or product malfunctions, or necessitate the forced cessation of cleanroom operations. Thus, steadfast adherence to proper gowning protocols emerges as a paramount imperative in sustaining the pristine environment and unblemished functionality of cleanrooms.
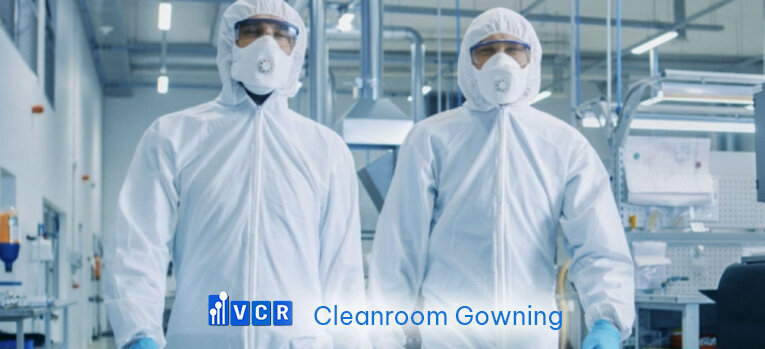
Step-by-Step Cleanroom Gowning Procedure
Cleanroom gowning protocols vary based on the cleanroom class and application. Frocks are suitable for ISO Class 7 or 8 cleanrooms, while ISO Class 5 or 6 requires coveralls, hoods, gloves, and booties. In sterile processing, utmost care is taken to prevent contact between sterile and non-sterile surfaces during gowning, processing, and cleaning.
Let us commence with the initial steps of the cleanroom gowning procedure, adhering to the following imperative guidelines:
1. Remove all makeup, perfume, and hair gels.
2. Take off personal items, including jewelry, car keys, and cell phones.
3. Clean street shoes or opt for designated cleanroom footwear.
4. Don shoe covers.
5. Enter the gowning room.
6. Thoroughly wash and dry your hands using a no-touch hand-washing and -drying station.
7. For ISO 6 or cleaner environments, don under gloves or glove liners and sanitize gloves.
8. Don a bouffant cap, followed by the facemask (beard guards for individuals with beards).
9. Retrieve garments from the cleanroom garment and supplies cabinet.
10. Don the necessary equipment, commencing from the head and proceeding towards the feet.
11. Put on the cleanroom hood.
12. Don your coverall, utilizing a clean gowning bench or lean-rail for support.
13. Don cleanroom-rated boots or shoes if specified.
14. Don goggles if specified.
15. Don cleanroom gloves, ensuring any specified adjustments to glove liners and disinfection are carried out prior to donning the gloves. Booties and gloves should overlap the coverall.
16. Conduct a final visual self-inspection before entering the cleanroom to ascertain no omissions have occurred.
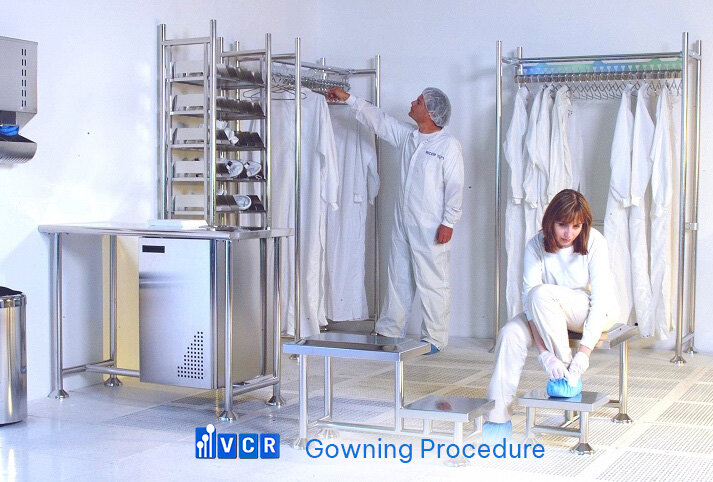
Note: Principles for Preventing Contamination During Cleanroom Gowning:
- Strictly adhere to the principle of isolating clean surfaces from any contact with contaminated ones.
- Exercise utmost care to keep garments entirely clear of any contact with unclean surfaces, such as the floor or any other potentially contaminated areas.
- Prioritize hand hygiene by refraining from handling clean garments or materials until a thorough handwashing process has been diligently carried out.
- Systematically initiate the gowning process from the highest point of the body and methodically progress downwards, ensuring an orderly approach to minimize the risk of contamination.
Read More: Cleanroom Classifications (Iso 8, Iso 7, Iso 6, Iso 5)
How to Design Gowning Room and Gowning Room Furniture Specifications
Gowning Rooms Classified
The efficacy of a well-constructed gowning room lies in its ability to establish a discernible demarcation between the pristine and contaminated floor areas. However, it is essential to recognize that not all facilities necessitate a dedicated gowning area endowed with ISO-rated partitions to ensure optimal performance.
In certain laboratory setups or pharmacy cleanrooms, the design of the gowning room may be more straightforward, comprising a mere floor demarcation to define the gowning space. In such cases, as the gowning room remains unsegregated from the cleanroom by interior partitions, it becomes imperative that the gowning equipment employed meets or surpasses the ISO class rating designated for the cleanroom itself, rather than conforming solely to the ISO rating assigned to the gowning room.
Conversely, in traditional cleanroom designs characterized by the presence of wall partitions demarcating the cleanroom from the gowning room, a distinct classification disparity is typically observed. The interior cleanroom classification is often one ISO class lower (i.e., cleaner) than the external gowning cleanroom. Consequently, an ISO 7 cleanroom partnered with an ISO 8 gowning room would entail the utilization of ISO 8-rated furniture within the gowning room to ensure harmonious alignment with the overall cleanroom standards.
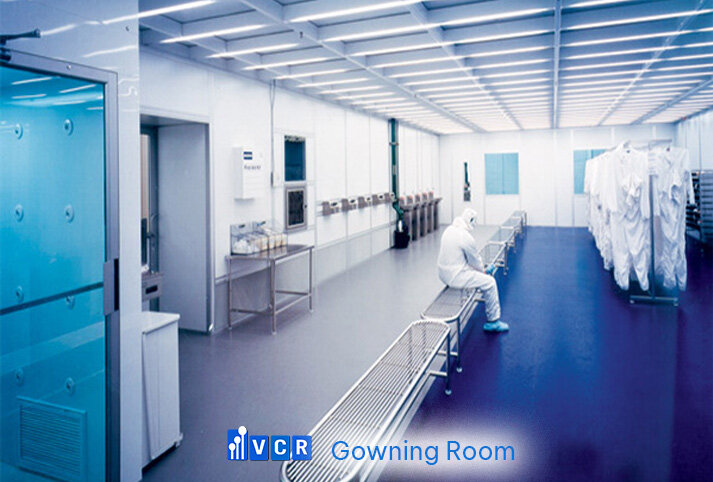
Gowning Room Furniture
- Gowning Platforms & Lean Rails: A gowning bench always separates the clean side from the dirty side
- Double-Sided Cleanroom Lean Rails: Cleanroom lean rails offer an easy-to-clean, ergonomic gowning station, minimizing shift-change congestion. Operators can safely balance on the rail while donning coveralls without the need to sit down or balance on one foot.
- Gowning Mirrors
- Gowning Room Dispensers
- Cleanroom Gown Storage Cabinets
- Cleanroom Pass Box: Reducing foot traffic in cleanrooms is crucial to limit contamination. Gowning room designs with pass-through chambers help minimize entry and exit, ensuring more reliable room air pressure control.
- Automatic Cleanroom Shoe Cleaning Machines
- Stainless Steel Crash Rails
Best Practice For Cleanroom Gowning
Best Practices for Donning Cleanrooms Gloves
You Should:
- Utilize sterile gloves specifically designed for cleanroom and aseptic processing, strictly avoiding the use of powdered gloves.
- Ensure hands are thoroughly dried before donning gloves.
- Don the dominant hand first to facilitate a smooth and efficient process.
- Opt for a wall-mounted consumable dispenser for streamlined access, reducing unnecessary movement.
You Shouldn't:
- Wear jewelry, fingernail polish, or cosmetics while donning cleanroom gloves.
- Refrain from waving gloved hands to accelerate the drying process after applying alcohol solutions.
- Never allow a gloved hand to come into contact with exposed skin to maintain strict hygiene and minimize contamination risks.
USP 797 Personnel Cleansing and Garbing Best Practices
You Should:
- Involve employees in the quality assurance process, ensuring open communication regarding hygiene evaluations.
- Prioritize meticulous hand cleansing in the anteroom before donning non-shedding gowns.
- Provide properly fitting garments for operators of all body sizes.
- Thoroughly wash hands and forearms up to the elbows with either non-antimicrobial or antimicrobial soap for at least 30 seconds in the ante area.
- Begin by covering the dominant hand first during gowning.
You Shouldn't:
- Avoid using scrub brushes on the hands, as they can cause skin damage and increased skin shedding.
- Refrain from using any type of drying wipe except disposable wipes or electronic hand dryers with HEPA filtration.
- Never don a gown before completing proper hand hygiene, as splashes while wearing non-shedding gowns can lead to microbial contamination.
- Ensure no contact between clean and dirty surfaces.
- Prevent clothes from touching the floor.
- Avoid using powdered gloves.
- Refrain from wearing jewelry, nail polish, or cosmetics.
- Never touch open skin with gloved hands to maintain strict hygiene and prevent contamination..
Finally, the selection of appropriate cleanroom gowning supplies and equipment constitutes a fundamental element in the effective management of cleanroom contamination. While this informational guide provides valuable insights, it must be emphasized that consulting with a knowledgeable cleanroom engineering consultant, well-versed in your unique equipment requirements and classification specifications, remains paramount. Their expertise ensures the optimal implementation of tailored solutions to suit your cleanroom's specific demands and guarantees a pristine and controlled environment.
The comprehensive insights and information pertaining to Cleanroom Gowning and the Gowning procedure, which have been elucidated, are poised to serve as a valuable resource in guiding and enhancing your endeavors concerning the utilization of clean rooms.
Brian