A Bag-In/Bag-Out (BIBO) setup consists of several interconnected parts that work together to maintain a sealed environment during filter changes. These components not only support containment but also streamline the entire replacement process, ensuring minimal downtime and maximum safety.
At the heart of any BIBO system is the filter housing. Typically constructed from durable materials such as stainless steel or coated metals, the housing must form an airtight seal to contain hazardous particles. Gaskets, clamps, and secure doors are crucial here. They prevent any gaps or weak points where contaminants could escape. In many facilities, the filter housing is designed with easy-to-open access panels, which help operators replace filters without compromising the cleanroom’s integrity.
The “bag” portion of Bag-In/Bag-Out refers to the specialized enclosure into which the used filter is drawn during replacement. These bags are often made of polyethylene or PVC - materials chosen for their tear-resistant properties and chemical compatibility. Depending on the level of hazard in the environment, the bags can be single - or multi-layered for added protection. Collars or clamps at the point where the bag attaches to the housing ensure a tight seal. This seal is essential: even the most advanced filter housing is ineffective if the connection to the bag is not secure.
Leak-proof, hinged doors allow technicians to access the filters when necessary. These doors are fitted with reliable locking mechanisms and airtight gaskets to maintain containment at all times. In some cases, observation windows or viewing ports are built into the doors. These windows let operators visually check bag integrity or confirm a proper seal without having to open the system. By minimizing the need for unnecessary openings, the risk of contamination breaches is further reduced.
To facilitate safer and more efficient filter changes, several additional tools can be incorporated into a BIBO system. Glove ports enable technicians to handle contaminated materials directly through the sealed bag, eliminating direct contact with hazardous particles. Sealing devices - such as thermal sealers or clamp-based solutions - ensure that once the old filter is removed, it can be fully contained before disposal. Pressure or vacuum gauges are also common, providing real-time data to verify that the housing and bag remain tightly sealed.
Depending on the specific requirements of a facility, a BIBO system might include decontamination ports for introducing disinfectants or sterilants before or after the filter swap. Interlocking doors add another layer of security, making accidental openings virtually impossible. Additionally, some systems come with built-in alarm functions that activate if pressure differentials exceed safe parameters. These optional features cater to environments where even minute contamination risks must be mitigated, ensuring that each aspect of the filter change process is controlled from start to finish.
IV. Step-by-Step: Safe Filter Changes Using BIBO
A successful Bag-In/Bag-Out (BIBO) filter change hinges on careful planning, meticulous execution, and thorough follow-up checks. From personnel training to final verification, each stage is designed to protect individuals and the environment from hazardous contaminants. Below is a detailed look at each step in the BIBO filter change process.
Pre-Change Preparations
Before initiating a filter change, it is vital to establish a safe and organized environment. All personnel involved should be fully trained on standard operating procedures (SOPs), which outline the precise sequence of actions required for a secure swap. Proper use of personal protective equipment (PPE) is another key element; gloves, respirators, and goggles help safeguard staff from potential exposure to hazardous particles.
An equipment check is also a must. The replacement filter needs to be free of defects, and the bag that will be used during removal should be inspected for rips or weaknesses. Clamps, collars, and any ancillary tools (like sealing devices) must be ready and functional. Lastly, confirm that the cleanroom setup is correct for the task at hand. Verify the airflow direction—whether negative or positive pressure is in use—and ensure ventilation systems are operating within safe parameters. Any abnormalities at this stage could compromise the entire process, so taking time for a thorough review can save significant trouble later.
Bag-In Phase
With all preparatory steps in place, the next focus is the Bag-In phase. The goal here is to secure the new bag to the filter housing in a way that completely isolates it from the external environment. Begin by aligning the bag’s open end around the housing door or collar, using clamps or specialized collars to form an airtight seal. A snug fit is crucial; even a small gap can allow dangerous materials to escape during the swap.
Once the bag is attached, a brief integrity check should be performed. This might involve a visual inspection to look for wrinkles or gaps, or in some cases, a minor pressure test to confirm that no air leaks are present. Ensuring the bag is firmly attached and leak-free lays the groundwork for a smooth and risk-free transition to the next phase.
Removing the Old Filter
With the bag now attached, the filter housing can be opened under controlled conditions. This step is often the riskiest because it is the moment when the used filter - potentially laden with contaminants - is exposed inside the housing. Therefore, it should be done slowly, allowing airflow systems to manage any potential release of particles. Depending on the specific setup, cleanrooms may use negative or positive pressure to keep contaminants contained.
Carefully pull the used filter from its slot and guide it directly into the sealed bag. Operators might utilize glove ports within the bag to manipulate the filter without exposing their hands to the hazardous material. Some environments may also require an intermediate decontamination step, where the housing interior is sprayed or fogged with a sterilant before proceeding. Any chemical or disinfectant used must have sufficient contact time to neutralize contaminants effectively. This extra measure is especially important in high-biosafety-level settings, such as BSL-3 or BSL-4 labs.
Bag-Out Phase
The Bag-Out phase finalizes the removal of the old filter from the cleanroom. Once the used filter is fully within the bag, the next step is to seal it securely. This can be done via twist ties, clamp-based seals, or a thermal sealing method. In scenarios involving highly hazardous or infectious materials, double-bagging may be advised. A second layer of containment further reduces the risk of accidental leakage during transport.
With the contaminated filter now contained, it can be detached from the housing. Carefully remove the bag from its collar or clamp, ensuring no gaps form in the process. The sealed bag is then transferred to the designated waste disposal area—usually a biohazard bin, chemical waste container, or other specialized receptacle, depending on the nature of the contaminants. Throughout this entire Bag-Out step, operators must remain vigilant for any tears or unforeseen leaks; if such issues arise, the emergency procedures outlined in the SOPs should be followed immediately.
Installing the New Filter
After disposing of the old filter, attention turns to placing the new one. Begin by inspecting the replacement filter to confirm it is compatible with the housing and free from damage. The orientation of the filter is critical; many filters have directional arrows that indicate airflow. Installing the filter backward can lead to reduced performance or possible damage to the filter media.
Slide the filter into position within the housing, ensuring it sits securely against the gaskets or other sealing surfaces. Double-check clamps and fasteners, verifying that the unit is tightly sealed. Finally, close the housing door and engage any locking mechanisms. Operators should listen and feel for a tight “seal” to confirm everything is properly secured.
See our Bag in Bag out Filter System here
Verification and Final Checks
No BIBO filter change is complete without thorough verification. First, check your airflow or pressure gauges to ensure they return to normal operating levels. If your cleanroom design includes alarms for high or low pressure, confirm they remain silent - no warnings should be triggered at this stage.
It is also essential to document the entire process. Record the date and time of the filter change, the name or ID of the operator(s), and any relevant details about the filter itself (such as batch number or part ID). Proper record-keeping is not only a best practice for traceability; it may also be a regulatory requirement in many industries.
By following each of these steps with precision, cleanroom operators can confidently swap out filters while mitigating risks. Bag-In/Bag-Out systems, when used correctly, make it possible to handle even the most hazardous materials in a safe, efficient manner. Through structured planning, careful preparation, methodical execution, and final checks, the entire filter change process can be completed with minimal downtime and maximum protection for both personnel and the environment.
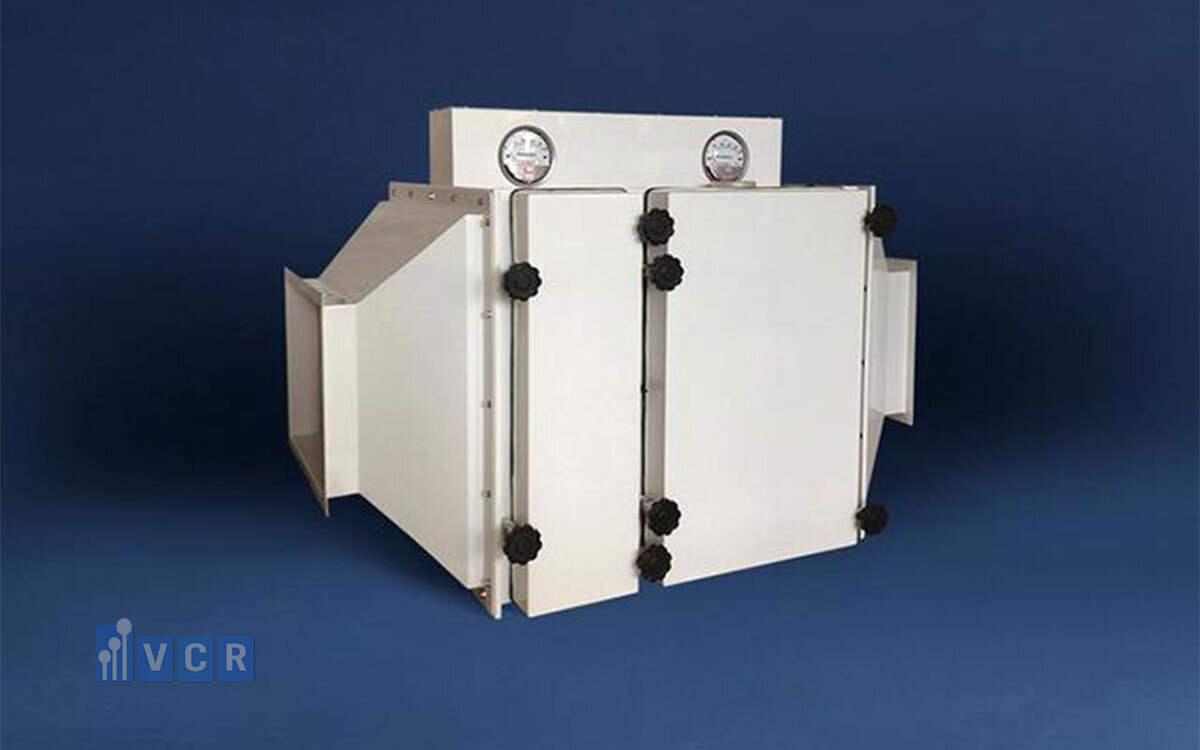
V. Safety Precautions and Best Practices
When it comes to Bag-In/Bag-Out (BIBO) operations, adhering to established safety protocols is essential for protecting both personnel and the broader facility. Even the most sophisticated BIBO systems can fail if best practices are not consistently followed, so understanding and implementing these measures is crucial for all involved.
1. Personal Protective Equipment (PPE)
Proper selection and use of PPE form the first line of defense against potential hazards. Depending on the risk level, personnel may need respirators, goggles, and full-body protective garments - particularly in environments dealing with highly infectious or toxic substances. Donning and doffing procedures should be carefully observed to avoid contamination; for instance, gloves should be put on last and removed first to minimize exposure. Training on correct PPE usage significantly reduces the likelihood of accidental contact with contaminants.
2. Risk Assessment
Before any filter change, it is important to evaluate the types of hazards present - whether chemical, biological, or radiological. Each of these risks may require different containment or decontamination measures, as well as alignment with specific Biosafety Level (BSL) requirements. In BSL-2 settings, for example, standard precautions and PPE might suffice, while BSL-4 labs require fully enclosed suits and airtight connections. Matching the protective measures to the identified risks ensures that personnel and processes are adequately safeguarded.
3. Emergency Procedures
Even in the best-managed facilities, unforeseen incidents can occur. A tear in the bag or a spill of potentially hazardous materials demands immediate and coordinated action. Operators should halt any ongoing work, isolate the affected area, and execute the established decontamination protocols. Prompt reporting is also essential, both for internal documentation and regulatory compliance. By following a clearly defined chain of response, facilities can minimize the impact of accidents and return to safe operation more rapidly.
4. Common Mistakes to Avoid
One of the most frequent pitfalls is rushing the BIBO process. Skipping vital steps such as double-checking seals or ensuring the correct orientation of new filters can lead to costly errors. Additionally, using the wrong type of bag material or filter size can compromise the entire containment process. Detailed pre-change checks, careful adherence to instructions, and ongoing vigilance help prevent these missteps.
5. Checklists and SOPs
Establishing standardized checklists and Standard Operating Procedures (SOPs) can go a long way toward ensuring consistency and reducing human error. By following a documented sequence of actions - from pre-change inspections to final verification - operators are less likely to forget critical steps or deviate from established safety protocols. These checklists should be regularly reviewed and updated to reflect new information, equipment changes, or evolving regulatory requirements.
Incorporating these precautions into every Bag-In/Bag-Out procedure not only protects individuals but also maintains the integrity of the cleanroom and surrounding facilities. With the right combination of PPE, risk assessment, emergency preparedness, diligent process execution, and robust SOPs, BIBO operations can be conducted with minimal risk and maximum efficiency.
VI. Maintenance, Inspection, and Troubleshooting
Effective Bag-In/Bag-Out (BIBO) systems rely on consistent maintenance and vigilant inspections to ensure they continue functioning at peak efficiency. From visual checks to scheduled upkeep, a proactive approach can prevent minor issues from escalating into major risks.
1. Regular Inspections
One of the simplest but most important practices is to perform regular visual inspections of the bag, clamps, and seals. Look for any signs of wear, such as small tears or loose fittings, which could compromise containment. In addition, monitor pressure readings and airflow rates around the filter housing.
Fluctuations can indicate potential leaks or blockages, and prompt investigation may avoid further complications.
2. Scheduled Maintenance
Beyond day-to-day checks, establish a routine maintenance schedule based on the operational intensity of your cleanroom. For instance, facilities with continuous high-hazard processes might need more frequent filter changes and part replacements than those running only a few hours a day. During these scheduled intervals, inspect and replace worn gaskets, clamps, or door seals to prevent unexpected breaches. Regularly cleaning and disinfecting the housing interior also helps maintain a sterile environment.
3. Common Faults
Even the most meticulously operated system can experience issues. Bag punctures or misalignment during filter changes are among the most frequent problems, allowing contaminants to escape or clean air to bypass the filtration mechanism. Another challenge arises if filters are not fitted correctly—this can lead to performance shortfalls or leaks. Recognizing these common faults early allows for swift corrective action.
4. Troubleshooting Tips
For minor issues like small tears in the bag, patching kits or additional sealing clamps can provide a quick fix, though a complete bag replacement may still be advisable if the damage is extensive. Recalibrating clamps and collars can solve minor alignment problems. However, if repeated failures or recurring leaks occur, it may be time to consult the original equipment manufacturer (OEM) or service experts. Their specialized insight can diagnose deeper problems that routine checks might miss.
5. Documentation
Finally, thorough record-keeping underpins the entire maintenance and troubleshooting process. Accurate logs of each filter change, inspection, and repair not only aid in audits and regulatory compliance but also help track patterns over time. This traceability enables proactive decision-making—such as ordering new parts before old ones fail—and supports continuous improvement in overall system reliability.
VII. Real-World Applications and Case Studies
Bag-In/Bag-Out (BIBO) systems find use in a wide range of industries and scenarios, particularly where contamination control is paramount. From pharmaceutical plants to high-level biosafety labs, the advantages of a sealed, controlled filter change process are both practical and measurable.
Pharmaceutical Manufacturing
In the production of sterile injectables or the handling of potent compounds, even minor contamination can have serious consequences. By employing BIBO systems, pharmaceutical companies can protect both product purity and worker safety. This method supports current Good Manufacturing Practice (cGMP) compliance by minimizing the risk of cross-contamination between batches. Whether it’s for biologics, vaccines, or highly potent oral dosage forms, BIBO maintains consistent sterility levels, thereby upholding stringent regulatory standards while also reducing the likelihood of costly production downtime.
Biosafety Labs
Biosafety Level (BSL) laboratories—particularly BSL-3 and BSL-4—handle some of the most dangerous pathogens known. Here, BIBO plays an integral role in preventing the accidental release of infectious agents during filter changes. Technicians can safely remove and replace contaminated filters without risking a lab-wide breach. Since these facilities often conduct critical research on emerging diseases, any lapse in containment can have serious public health implications. Through BIBO, labs maintain rigorous isolation protocols, preserving both research integrity and operator safety.
Chemical and Nuclear Industries
In large-scale chemical or nuclear plants, airborne hazards can include toxic fumes, radioactive dust, and other dangerous materials. BIBO systems act as a frontline defense, confining these contaminants and helping to keep workers out of harm’s way. This rigorous approach is especially valuable in scenarios where a single incident could lead to substantial environmental harm or widespread exposure. By integrating Bag-In/Bag-Out into their operational procedures, chemical and nuclear facilities improve overall safety and regulatory compliance while maintaining efficiency.
Case Studies
Real-world examples underline the effectiveness of BIBO in diverse settings. Some facilities report substantial cost savings after adopting Bag-In/Bag-Out, citing reduced cleanup expenses and fewer production delays. Others highlight a dramatic decrease in contamination incidents, reinforcing the argument that investing in reliable containment pays off both financially and operationally. Lessons learned from successful BIBO implementations range from the importance of thorough training to the value of robust maintenance schedules, all contributing to a safer and more efficient working environment.
VIII. Regulatory and Compliance Considerations
Regulatory requirements play a significant role in how Bag-In/Bag-Out (BIBO) systems are designed, implemented, and maintained. Various governmental and international bodies—such as the FDA (Food and Drug Administration), OSHA (Occupational Safety and Health Administration), EPA (Environmental Protection Agency), and their counterparts worldwide—provide guidelines that influence every aspect of filter change procedures. These regulations often include specific mandates on documentation, labeling, and operational oversight, ensuring that health, safety, and environmental standards are consistently upheld.
Facilities handling pharmaceuticals, medical research, or high-risk contaminants typically operate under frameworks like current Good Manufacturing Practice (cGMP), ISO standards, or Biosafety Level (BSL) guidelines. BIBO systems support these standards by offering a defined, sealed process for handling potentially hazardous materials. Standard Operating Procedures (SOPs) detailing each step of the BIBO process, thorough labeling of filter housings and bags, and regular inspections are common requirements. Meeting these benchmarks helps protect both staff and the environment from contamination risks.
Audit readiness is also a major consideration. Regulatory agencies and certifying bodies often conduct inspections to verify whether facilities comply with the stipulated guidelines. During such audits, inspectors look for evidence of proper record-keeping—such as detailed logs of filter changes, maintenance actions, and any incident reports. Demonstrating clear, consistent adherence to BIBO protocols not only meets legal obligations but also builds confidence among stakeholders, ensuring that products and research outcomes remain safe, reliable, and globally acceptable.
IX. Future Trends in BIBO Technology
As cleanroom requirements become more stringent and sustainability goals gain momentum, Bag-In/Bag-Out (BIBO) technology continues to evolve. One promising area involves the development of new bag materials—ranging from biodegradable plastics to antimicrobial or ultra-strong synthetic films. These innovations aim not only to enhance safety and durability but also to address environmental concerns by reducing plastic waste.
Another key trend lies in automation and smart monitoring. Some facilities have begun integrating IoT-enabled sensors that provide real-time data on pressure levels, airflow, and even bag integrity. Such systems can detect early warning signs—like slight pressure drops or temperature fluctuations—alerting operators before a full-scale leak or filter failure occurs. Remote monitoring capabilities also allow for quick troubleshooting, saving time and labor while maintaining high safety standards.
In terms of user safety, advanced designs feature interlocking doors that eliminate the chance of accidental openings mid-process. These systems further enhance containment by preventing human error, a major source of contamination breaches. Advanced filters, often manufactured with specialized coatings or antimicrobial treatments, round out the improvements in safety and efficiency.
However, integrating these upgrades into existing workflows presents challenges. Balancing the cost of new technology against operational budgets remains a recurring concern, as does gaining regulatory acceptance for novel materials or automated processes. Despite these hurdles, ongoing R&D in BIBO technology holds the potential to significantly improve both the safety and sustainability of cleanroom operations in the years to come.
X. Conclusion
BIBO (Bag-In/Bag-Out) stands as a cornerstone in ensuring safe and efficient filter changes within high-containment environments. By following essential steps—Bag-In, Bag-Out, decontamination, and verification—cleanroom operators can significantly reduce the risk of exposure to hazardous materials while maintaining stringent standards of product integrity. Each phase of the process is designed to create multiple layers of containment, preventing contaminants from escaping and protecting both personnel and the broader facility.
Over the long term, embracing BIBO yields substantial benefits. Enhanced safety measures not only safeguard staff from harmful substances but also help organizations avoid costly contamination incidents or regulatory penalties. Maintaining a robust Bag-In/Bag-Out protocol often means smoother operations overall, thanks to reduced downtime for post-change decontamination and fewer disruptions from accidental leaks or spills.
Looking ahead, BIBO technology continues to evolve in response to emerging challenges and opportunities. Innovations in bag materials, automation, and real-time monitoring are steadily improving containment reliability and sustainability. Ultimately, whether a facility is newly implementing BIBO or refining existing procedures, investing in advanced safety protocols offers lasting value. By adopting or upgrading Bag-In/Bag-Out methods, organizations reinforce their commitment to worker protection, regulatory compliance, and the highest standards of contamination control for years to come.
PN