Validation and Qualification of Pass Box in GMP Facilities
Pass Box play a pivotal role in the pharmaceutical industry, functioning as small, enclosed structures that facilitate the transfer of materials between separate cleanroom areas or between rooms of different contamination risk levels.
- I. Introduction
- II. Fundamentals of Pass Box Operation
- III. Understanding Validation and Qualification
- IV. Installation Qualification (IQ)
- V. Operational Qualification (OQ)
- VI. Performance Qualification (PQ)
- VII. Performance Acceptance Criteria in Detail
- VIII. Common Deviations and Failures
- IX. Documentation and Record-Keeping
- X. Conclusion
I. Introduction
Pass Box play a pivotal role in the pharmaceutical industry, functioning as small, enclosed structures that facilitate the transfer of materials between separate cleanroom areas or between rooms of different contamination risk levels. In essence, they serve as a controlled gateway designed to maintain strict cleanliness standards during the movement of products and components. By minimizing physical traffic, Pass Box reduce the influx of particles and other contaminants that could compromise product quality and patient safety. Although seemingly simple in concept, Pass Box requires meticulous design, validation, and ongoing oversight to ensure they meet stringent regulatory requirements in Good Manufacturing Practice (GMP) environments.
A. Overview of Pass Box in GMP Facilities
Definition and Primary Function
Historically, Pass Box emerged as a practical solution to enhance the overall contamination control strategy in cleanroom. Their core purpose is to provide an airlock-like zone where materials can be placed on one side and retrieved from the other without unnecessarily opening the main cleanroom doors. This controlled transfer mechanism is critical when different classified areas (e.g., ISO Class 7 vs. ISO Class 8) or separate containment levels (sterile vs. non-sterile) must be maintained.
Read more: Cleanroom Standard Classification
Importance in Aseptic Processing
In aseptic manufacturing, minimizing the potential for airborne or surface-borne contamination is of paramount importance. Pass Box help reduce foot traffic and prevent cross-contamination by limiting personnel movement between cleanrooms. They interface seamlessly with standard aseptic techniques—ensuring that materials, once sterilized, remain in a protected environment throughout transport. As such, Pass Box bolster the overall contamination control strategy, offering an additional safeguard that supports the maintenance of critical cleanroom conditions.
Objective of Validation and Qualification
In GMP facilities, every piece of equipment that can impact product integrity must undergo rigorous validation. For Pass Box, the objective of validation and qualification revolves around demonstrating their ability to function consistently within specified design parameters. By verifying their performance, engineers and quality assurance teams ensure that the Pass Box continuously meet cleanliness requirements, pressure differentials, and interlock functionalities. Ultimately, robust validation safeguards product quality and patient well-being.
B. Purpose and Scope of the Article
Target Audience
This article is primarily aimed at pharmaceutical engineers, validation specialists, and quality professionals who are involved in the design, implementation, and maintenance of Pass Box. It will also benefit individuals who oversee regulatory compliance and conduct internal audits within GMP facilities.
Scope
The discussion encompasses best practices, regulatory expectations, and essential technical insights specific to Pass Box. It covers the entire qualification life cycle—including Installation Qualification (IQ), Operational Qualification (OQ), and Performance Qualification (PQ)—and how these activities align with overarching GMP requirements.
Limitations
While the principles outlined herein can be applicable to various industries, the focus remains on the pharmaceutical sector operating under cGMP guidelines. Non-pharmaceutical Pass Box, such as those used in food processing or general manufacturing, are beyond the scope of this article.
C. Regulatory Framework
Key GMP Guidelines
Compliance with GMP regulations, particularly FDA’s 21 CFR Part 210/211 and EU GMP Annex 1, is a foundational requirement when designing and qualifying Pass Box. In addition, ISO 14644 standards outline the classifications for cleanroom environments, serving as a critical reference point for defining airborne particle limits and setting engineering controls.
Expectations for Pass Box Qualification
Regulators expect a risk-based approach that demonstrates how Pass Box consistently prevent contamination and maintain cleanroom integrity. This typically involves a series of tests verifying air velocity, recovery times, and interlocking systems. The end goal is to confirm that Pass Box does not pose contamination risks and function within precise performance parameters.
Roles of Regulatory Inspections and Audits
During inspections, regulatory bodies often scrutinize the qualification status and operational records of Pass Box. Inadequate validation can result in observations or warnings (e.g., FDA Form 483), emphasizing the importance of well-documented procedures, routine checks, and reliable evidence of continued compliance.
D. Definitions of Essential Terms
Cleanroom Classes
Pharmaceutical cleanrooms adhere to ISO classifications (e.g., ISO 5, 6, 7, 8), which dictate permissible particle counts. Pass Box must align with the classification requirements of adjoining areas, ensuring that no shift in cleanliness grade occurs during transfer.
Differential Pressure
Maintaining proper pressure gradients between higher-grade and lower-grade areas is vital to preventing the backflow of contaminants. Pass Boxes are designed to support these gradients, and their performance during transfers must be confirmed and periodically monitored.
Viable and Non-Viable Particulates
Both viable (microbial) and non-viable (dust, debris) particles can threaten product sterility. Qualification studies typically measure these parameters to confirm the Pass Box’s ability to maintain the desired cleanliness levels during normal operation.
By establishing these foundational concepts, this article will delve deeper into the life cycle approach of validating and qualifying Pass Box - covering IQ, OQ, PQ protocols, performance acceptance criteria, common pitfalls, and the documentation required to meet GMP standards. Through this structured exploration, readers will gain the insight necessary to implement robust Pass Box validation strategies that uphold product quality and ensure patient safety.
II. Fundamentals of Pass Box Operation
Pass Box serves as critical conduits in GMP facilities, enabling the controlled movement of materials in and out of cleanrooms. Their successful operation depends on a thorough understanding of cleanroom design principles, airflow control, and contamination prevention. Equally important are the different types of Pass Box available - each suited for specific manufacturing needs - and their typical applications in pharmaceutical environments. This section explores the foundational elements of Pass Box operation, highlighting why validation is key to ensuring consistent performance and compliance with regulatory standards.
Read more: How to choose the right Pass Box for cleanroom?
A. Cleanroom Basics
1. Airflow Dynamics
One of the cornerstones of cleanroom design is airflow control, which encompasses both laminar and turbulent flow patterns.
- Laminar Flow: Characterized by a unidirectional, uniform velocity airflow that sweeps away particles in a predictable manner. In laminar flow hoods or dynamic Pass Boxes, high-efficiency particulate air (HEPA) filters purify incoming air. This filtered air then moves straight downward or horizontally at a consistent velocity, preventing particles from recirculating.
- Turbulent Flow: In rooms or zones without laminar flow systems, air tends to mix more freely. While modern GMP facilities minimize turbulent areas, some ancillary spaces may still experience turbulence, raising the risk of contamination dispersal.
When a Pass Box is installed, it must integrate with the existing Heating, Ventilation, and Air Conditioning (HVAC) system so that the pressure differentials remain consistent across adjoining areas. This ensures that opening a Pass Box does not disrupt the delicate balance that keeps particles from migrating into higher-grade cleanroom zones.
Read more: The differences between cleanroom HVAC system and other HVAC systems
Maintaining Pressure Gradients
Cleanrooms are generally designed with a cascade of pressures - higher in more critical areas and lower in less critical areas. Pass Boxes function somewhat like airlocks, preventing sudden pressure drops or surges when materials move between zones. If the pressure differential is not maintained properly, particles from a less clean area can be drawn into a more sensitive area, posing a contamination risk. By design, Pass Boxes often include interlocking doors, which help preserve these differentials by preventing simultaneous door openings.
2. Particle Generation and Control
Despite meticulous design, particles are inevitably introduced into a cleanroom environment through various sources:
- Operators: Humans shed skin cells and hair, and even the slightest movement can release particulates.
- Materials: Packaging materials, raw substances, and equipment can carry dust or microbes.
- Equipment: Mechanical systems, including conveyors or machinery, generate wear particles.
The role of Pass Boxes in controlling particle transfer is twofold. First, they reduce foot traffic—by limiting the number of times personnel must exit and re-enter a cleanroom, the overall risk of contamination is lowered. Second, advanced Pass Boxes (especially dynamic designs) include dedicated filtration and pressure control mechanisms, actively removing or trapping particulates before they can move from one area to another. This is particularly beneficial in aseptic manufacturing, where even slight contamination can compromise an entire batch.
B. Types of Pass Box
1. Static Pass Box
Static Pass Box is the most straightforward design. They:
- Rely on Ambient Conditions: No internal fan or airflow system is present; instead, they depend on the cleanliness and pressure differentials already established in the adjoining rooms.
- Ideal for Moderate-Level Cleanrooms: Since static Pass Boxes do not actively filter or condition the air inside, they are typically used between areas that have similar cleanliness classifications (e.g., ISO 8 to ISO 8) or where the risk of contamination is comparatively low.
- Lower Cost and Simpler Maintenance: Fewer components mean reduced maintenance overhead, making static Pass Boxes a cost-effective choice in certain operations.
However, static Pass Boxes are less effective in scenarios that demand stringent contamination control, such as high-risk or aseptic processes. They also rely heavily on proper door interlocks and existing cleanroom pressure balances to function effectively.
2. Dynamic Pass Box
Dynamic Pass Box is equipped with:
Integrated HEPA Filters, Blower Systems, or Laminar Flow: These components create a controlled airflow environment within the Pass Box, often at an ISO Class 5 or 7 level, depending on the design.
- Greater Control Over Contamination: Because the interior is positively pressurized with filtered air, contaminants are actively pushed out or trapped, thereby preventing migration between rooms.
- Application in High-Risk Areas: Dynamic Pass Boxes are particularly valuable in handling potent substances, sterile APIs (Active Pharmaceutical Ingredients), or other sensitive materials that require stringent contamination safeguards.
These advanced features come with a higher initial investment and more complex maintenance requirements (e.g., regular filter testing, calibration of airflow sensors). Nonetheless, the enhanced control capabilities make them a preferred choice in many aseptic or high-potency operations.
3. Custom/Hybrid Designs
Beyond standard static or dynamic models, custom or hybrid Pass Boxes may include specialized features such as:
- UV Sanitization: Installing UV-C lamps inside the Pass Box to reduce microbial load on surfaces.
- Vaporized Hydrogen Peroxide (VHP) Systems: Automated sanitization cyclesthat expose the interior to sterilizing vapors, suitable for stringent aseptic processes.
- Application-Specific Designs: Certain handling requirements—like cytotoxic or highly potent compounds—necessitate additional containment measures, specialized materials of construction, or integrated wash-down features.
While custom Pass Boxes typically address unique risks in specialized manufacturing environments, they also demand robust validation to confirm the effectiveness of any added features.
C. Common Applications in GMP Settings
1. Material Transfer
The most frequent use of Pass Boxes is to transfer raw materials, in-process components, and finished products between adjacent cleanroom zones. By doing so, Pass Boxes minimize foot traffic and reduce the frequency of personnel gowning, helping maintain cleanroom integrity and lowering the risk of error or cross-contamination.
2. Workflow Optimization
Pass Boxes support lean manufacturing principles by streamlining workflows. Rather than routing personnel through multiple doors or relying on complex hand-offs, materials move quickly and directly through Pass Boxes. This efficiency can lower labor costs, reduce the likelihood of mishandling, and improve overall production throughput.
3. Waste Disposal
Certain Pass Boxes are designed specifically for waste management, allowing operators to safely discard used materials or contaminated packaging without needing to exit the controlled area. These specialized waste Pass Boxes often feature containment features (e.g., negative pressure, sealed doors) to protect workers and the environment.
D. Importance of Validation
1. Regulatory Requirement
In pharmaceutical manufacturing, any equipment with the potential to affect product quality must be validated. Pass Boxes, though sometimes considered secondary to primary processing equipment, are no exception. Regulators expect evidence - often through IQ, OQ, and PQ - that each Pass Box complies with GMP standards and operates within set specifications.
2. Quality Assurance
Validation not only meets a regulatory mandate; it also provides internal assurance that the Pass Box functions as intended. Regular monitoring and requalification confirm that design parameters remain intact, and that the Pass Box continues to protect products and processes from contamination risks.
3. Risk Mitigation
From a risk management perspective, properly validated Pass Boxes help reduce the chances of contamination-related failures. If a Pass Box were to malfunction - e.g., if an interlock failed, allowing both doors to open simultaneously - the impact could be substantial, ranging from product recalls to regulatory citations. Thus, ongoing validation is both a preventive measure and a pillar of good quality governance.
III. Understanding Validation and Qualification
A. The Validation Life Cycle
1. Concept and Definition
Validation is typically defined as “documented evidence that a process or equipment consistently operates according to predetermined criteria.” In a regulated environment, this means demonstrating - through systematic testing and documentation - that the Pass Box design, installation, and ongoing performance meet GMP standards. Unlike mere functional testing, validation focuses on consistency and repeatability: the Pass Box must work within defined limits under a variety of conditions, time after time.
2. Stages in Equipment Validation
Equipment validation in GMP manufacturing usually follows a sequential series of stages:
- Design Qualification (DQ): This phase confirms that the Pass Box’s design meets user and regulatory requirements. Key design elements - such as material of construction, airflow requirements, and interlock mechanisms - must align with the intended use and GMP guidelines.
- Installation Qualification (IQ): Once the Pass Box is installed, IQ verifies that it is placed and configured according to the approved design and specifications (e.g., correct positioning, proper utility connections, verified component materials).
- Operational Qualification (OQ): This stage tests whether the Pass Box operates within specified parameters under defined conditions (e.g., airflow velocity, interlock function, alarm systems).
- Performance Qualification (PQ): PQ demonstrates that the Pass Box consistently performs as intended under actual production conditions, accounting for real-world usage patterns and potential variations (like different shifts, material loads, and operating frequencies).
3. Continual Validation
Validation does not end after the PQ phase. Continual validation involves ongoing monitoring of critical parameters, periodic re-validation, and, if necessary, re-qualification. When significant changes occur - such as relocating the Pass Box, modifying filters, or upgrading control systems - further qualification ensures that the Pass Box continues to meet the original acceptance criteria or newly defined standards.
B. Role of IQ, OQ, PQ Specifically for Pass Boxes
- Equipment Installation: Verifying the Pass Box is correctly integrated into the cleanroom wall, that seals are intact, and utilities (if dynamic) are connected to the correct power supply or air sources.
- Documentation: Checking vendor manuals, serial numbers, and material certificates, ensuring these match the design specifications.
- Safety Features: Confirming door interlocks and emergency stops (if applicable) function as intended from a hardware standpoint.
Read more: Pass box installation guidelines
- Interlock Tests: Ensuring that only one door can open at a time, thereby maintaining pressure differentials.
- Airflow and Pressure Checks (if dynamic): Confirming HEPA filter functionality, airflow velocities, and pressure gradients.
- Alarm Systems: Verifying that alerts, such as open-door alarms or pressure loss notifications, trigger correctly.
C. Importance of Risk Assessments in Pass Box Qualification
- Door Seal Breaches: Allows unfiltered air to enter or escape.
- Inadequate Air Exchange: Could lead to particle buildup.
- Filter Failure: In a dynamic Pass Box, a damaged HEPA filter can jeopardize sterility.
D. Documentation Requirements
IV. Installation Qualification (IQ)
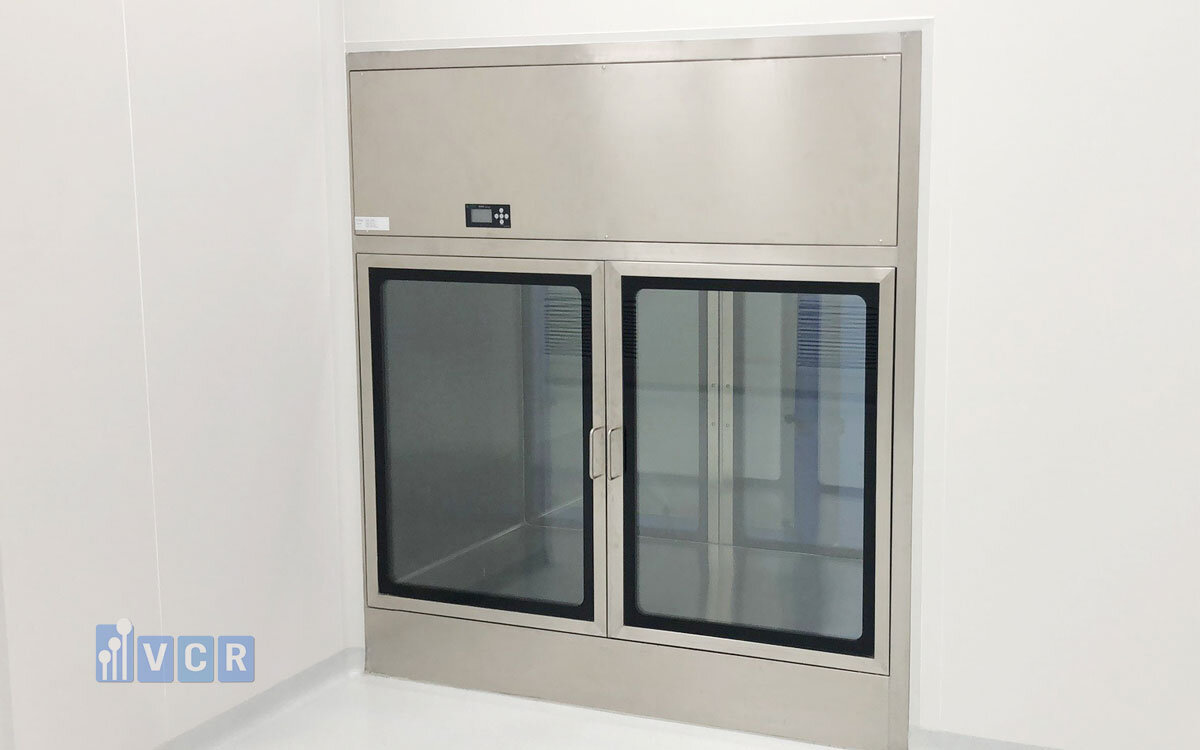
A. Goals of IQ
- Location Check: Ensuring the Pass Box is situated in the predetermined spot on the cleanroom wall or partition.
- Alignment: Checking that the Pass Box is level and that the doors align accurately for proper sealing and operation.
- Integration with Cleanroom Walls: Verifying any necessary bracketry, flush-mounted surfaces, or sealing materials are correctly installed to maintain the integrity of cleanroom classifications.
- As-Built Drawings: Cross-checking the physical unit against engineering drawings and vendor documentation.
- Utility Requirements: For dynamic Pass Boxes, confirming the unit receives the correct power supply voltage, appropriate airflow rate (if it has its own blower system), and proper grounding.
- Environmental Conditions: Ensuring the ambient temperature, humidity, and cleanroom classification of the installation area align with the Pass Box’s design parameters.
- Serial Numbers: For blowers, filters, and sensors, ensuring traceability if replacements or repairs become necessary.
- Material Certificates: Verifying that stainless steel or other construction materials conform to documented specifications (e.g., 304 vs. 316L).
- Manufacturer Specifications: Keeping vendor manuals, warranties, and service guidelines on file.
B. Prerequisites for IQ
1. Approved Design Specifications
A properly conducted IQ depends on having clear, approved design documents, such as a Design Qualification (DQ) or User Requirement Specification (URS). These documents provide the acceptance criteria and parameters by which the actual installation is evaluated. Without them, IQ activities lack objective measures for success.
2. Calibration of Measurement Instruments
Before starting the IQ, any tools or instruments used (e.g., pressure gauges, temperature sensors) must be calibrated and certified. This ensures accurate measurement of parameters like differential pressure or airflow during testing and eliminates the risk of false acceptance or rejection of equipment.
3. Qualified Installation Team
The installation team—whether composed of internal technicians, external contractors, or a mix—must possess relevant training and experience. They should be familiar not only with standard installation practices but also with GMP requirements. This expertise minimizes errors and expedites the validation process.
C. IQ Procedures
1. Physical Inspection
Teams perform a comprehensive visual and tactile inspection to confirm:
- Alignment and Seals: No gaps or misalignments that can compromise pressure or cleanliness.
- Finishing: Surfaces should be smooth, free of scratches or burrs that could harbor contaminants.
- Absence of Damage or Corrosion: Any signs of damage or rust must be addressed promptly.
2. Utility Checks
Utility verification is especially important for dynamic Pass Boxes:
- Power Supply: Verifying the correct voltage, amperage, and grounding.
- Blower System Connections: Checking that airflow lines, if applicable, are properly attached.
- Air Supply Lines: Confirming connections to the facility HVAC system or local HEPA filtration are secure and free from leaks.
3. Documentation Checks
Paperwork review is a significant portion of IQ. Technicians and validation staff compare:
- Equipment Tags: Ensuring the model and serial numbers match vendor documents.
- Vendor Manuals: Confirming installation steps align with manufacturer recommendations.
- Design Drawings: Verifying “as-built” installation matches engineering schematics.
4. Safety and Interlock Testing
A critical functional check during IQ is ensuring door interlocks work correctly:
- Single-Door Operation: Confirm that both doors cannot open simultaneously.
- Emergency Stop Systems: Testing any overrides or emergency release mechanisms to ensure occupant safety and compliance.
D. IQ Documentation and Acceptance Criteria
E. Common IQ Challenges
V. Operational Qualification (OQ)
Operational Qualification (OQ) is the second critical phase in the validation process of Pass Boxes within GMP facilities. While Installation Qualification (IQ) ensures that the Pass Box is correctly installed, OQ verifies that it operates according to its design specifications under simulated or typical operational conditions. This phase is essential to confirm that all functional aspects of the Pass Box perform reliably, maintaining the integrity of the cleanroom environment. This section delves into the goals of OQ, the specific testing and verification procedures involved, the performance acceptance criteria, environmental monitoring during OQ, documentation requirements, and common challenges encountered during this phase.
A. Goals of OQ
1. Verify Operational Parameters
The primary goal of OQ is to ensure that the Pass Box operates within its defined specifications under both simulated and typical load conditions. This involves testing the Pass Box’s ability to maintain appropriate airflow, pressure differentials, and overall functionality during regular and peak usage scenarios. By doing so, it is confirmed that the Pass Box can handle the demands of the production environment without compromising cleanroom standards.
Learn more about Pass Box Accessories.
2. Test Control and Monitoring Systems
OQ also focuses on evaluating the effectiveness of control and monitoring systems integrated into the Pass Box. This includes verifying that door sensors, interlock logic, alarm conditions, and indicator lights function correctly. These systems are crucial for maintaining operational integrity and ensuring immediate response to any deviations that could threaten contamination control.
3. Identify Operational Weak Points
Another essential objective of OQ is to identify any operational weaknesses within the Pass Box system. By conducting thorough testing, potential vulnerabilities—such as inconsistent airflow or faulty interlocks - are uncovered. Addressing these weak points ensures that the Pass Box operates reliably within its designed performance range, thereby safeguarding product quality and regulatory compliance.
B. Testing and Verification Procedures
1. Door Interlock Function
A critical component of OQ is the testing of door interlock mechanisms. This involves simulating multiple use cases where doors are opened and closed in various sequences to confirm that no cross-opening occurs. Effective interlock functionality ensures that both doors cannot be open simultaneously, thereby maintaining the necessary pressure differentials and preventing contamination ingress.
2. Alarm and Alert Systems
Validating alarm and alert systems is another key procedure in OQ. This includes testing pressure drop alarms, door open alarms, and other alert mechanisms to ensure they trigger appropriately under defined conditions. Proper functioning of these systems provides immediate notification of any operational issues, enabling swift corrective actions to maintain cleanroom integrity.
3. Airflow Verification (Dynamic Pass Boxes)
For dynamic Pass Boxes, airflow verification is paramount. This involves checking blower start-up times, ensuring filter integrity, and measuring velocity uniformity across the Pass Box. Consistent and reliable airflow is essential for maintaining the desired cleanroom classification and preventing particle accumulation or contamination.
C. Performance Acceptance Criteria
D. Environmental Monitoring During OQ
E. OQ Documentation and Acceptance Criteria
F. Common OQ Challenges
1. Inconsistent Airflow
Inconsistent airflow can stem from filter issues, fan motor performance problems, or inherent design flaws. Addressing these challenges typically involves recalibrating equipment, replacing faulty components, or redesigning airflow pathways to ensure uniform distribution.
2. Door Interlock Failures
Failures in door interlock systems may result from sensor misalignment, wiring errors, or flawed software logic. Regular maintenance, precise calibration, and thorough testing are necessary to ensure that interlocks function reliably, preventing simultaneous door openings.
3. Unstable Pressure Differentials
Unstable pressure differentials can be caused by fluctuations in the facility’s HVAC system or interference from additional equipment. Ensuring that the Pass Box is adequately integrated with the overall HVAC strategy and conducting regular pressure stability tests help mitigate these issues, maintaining consistent contamination control.
VI. Performance Qualification (PQ)
Performance Qualification (PQ) represents the final and crucial phase in the validation lifecycle of Pass Boxes within GMP facilities. While Installation Qualification (IQ) ensures that the Pass Box is correctly installed and Operational Qualification (OQ) verifies that it operates within specified parameters, PQ demonstrates that the Pass Box consistently performs as intended under real-world conditions. This phase confirms the Pass Box’s reliability, long-term functionality, and seamless integration with other processes, thereby ensuring sustained contamination control and regulatory compliance. This section outlines the goals of PQ, dynamic testing procedures, interfacing with the surrounding environment, long-term performance testing, documentation requirements, and common challenges encountered during PQ.
A. Goals of PQ
1. Demonstrate Consistent In-Use Performance
The primary objective of PQ is to validate the Pass Box’s performance under actual operating conditions. This involves conducting material transfers as they would occur during routine production, ensuring that the Pass Box maintains cleanliness standards consistently. By replicating normal usage scenarios, PQ confirms that the Pass Box effectively controls contamination and operates reliably during day-to-day operations.
2. Long-Term Reliability
PQ also aims to verify the Pass Box’s reliability over extended periods. This involves monitoring key performance parameters to ensure they remain within specified limits despite prolonged use. Assessing long-term reliability helps identify potential wear and tear, ensuring that the Pass Box continues to function correctly without frequent maintenance or unexpected failures.
3. Interaction with Other Processes
Another critical goal of PQ is to ensure that the Pass Box does not negatively impact adjacent rooms or manufacturing processes. This involves verifying that the Pass Box operates harmoniously within the broader cleanroom environment, maintaining proper pressure differentials and airflow patterns. Ensuring seamless interaction with other systems prevents cross-contamination and supports overall process efficiency.
B. Dynamic Testing
1. Load Simulation
Dynamic testing involves simulating typical load conditions to assess the Pass Box’s performance under realistic usage scenarios. This includes testing with standard load volumes and various material packaging types to ensure that the Pass Box can handle the expected throughput without compromising cleanliness or operational integrity. By replicating actual load conditions, PQ verifies that the Pass Box can manage the physical demands of production.
2. Worst-Case Scenarios
To thoroughly evaluate the Pass Box’s robustness, worst-case scenarios are simulated. These scenarios might include overloading the Pass Box, extended door open times, or high-throughput days. Testing under these extreme conditions ensures that the Pass Box can maintain performance standards even during peak usage or unexpected surges, thereby safeguarding against potential contamination or operational failures.
C. Interfacing with Surrounding Environment
D. Long-Term Performance Testing
E. PQ Documentation and Acceptance Criteria
F. Common PQ Challenges
VII. Performance Acceptance Criteria in Detail
A. Air Velocity
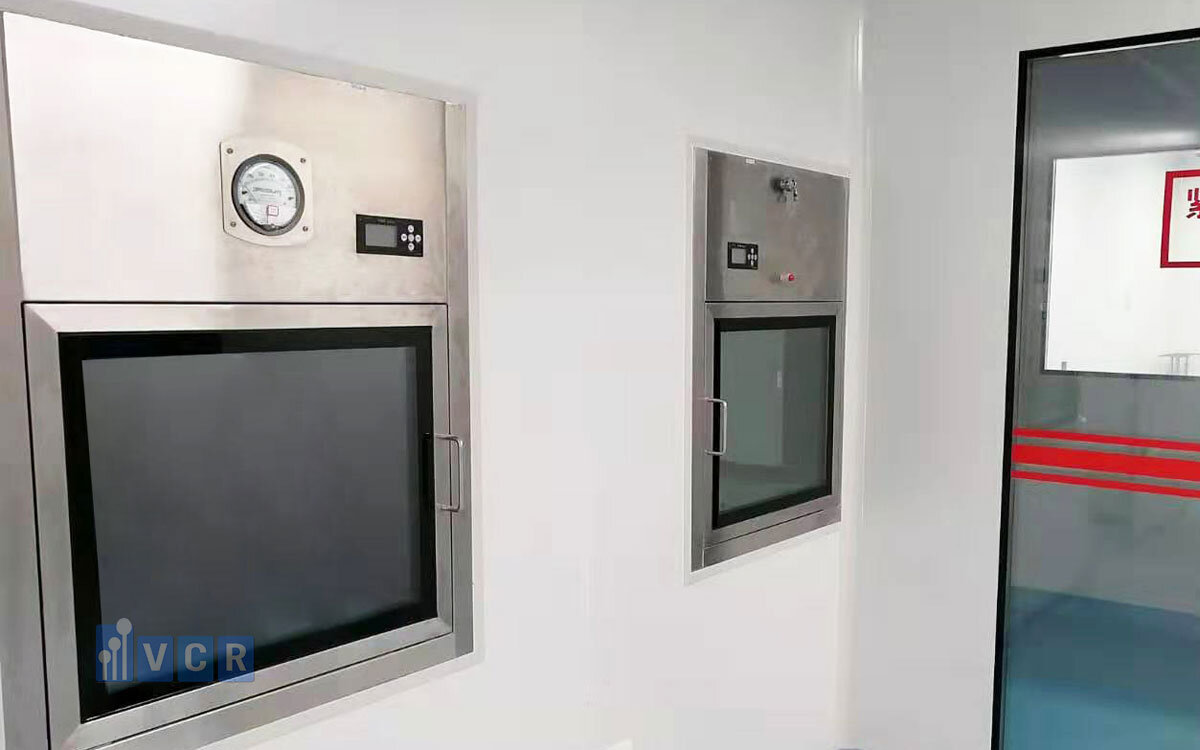
B. Recovery Time
C. Particle Counts
D. Pressure Differentials
E. Microbial Contamination Levels
F. Setting Tolerances
G. Impact of Regulatory Guidance
1. EU Annex 1 Updates
Recent updates to EU Annex 1 emphasize a comprehensive contamination control strategy, mandating robust qualification of all contamination control devices, including Pass Boxes. These updates require facilities to demonstrate how Pass Boxes contribute to maintaining aseptic conditions, reinforcing the need for stringent performance acceptance criteria.
2. FDA Guidance on Aseptic Processing
The FDA Guidance on Aseptic Processing provides recommendations for environmental monitoring and qualification of equipment like Pass Boxes. Adhering to these guidelines ensures that Pass Boxes meet the FDA’s expectations for contamination control, facilitating regulatory compliance and minimizing the risk of enforcement actions.
VIII. Common Deviations and Failures
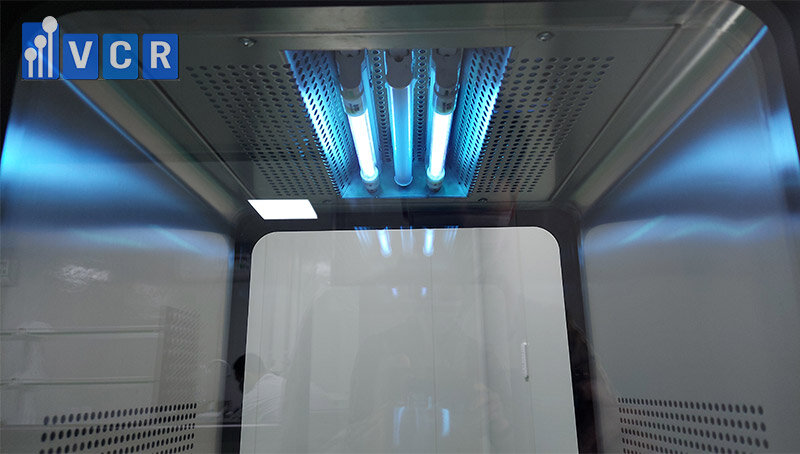
A. Types of Deviations
B. Root Cause Analysis
C. Corrective and Preventive Actions (CAPA)
D. Case Studies of Typical Failures
E. Preventive Measures to Avoid Recurrence
1. Proactive Maintenance
Implementing proactive maintenance schedules, including regular filter changes, sensor calibrations, and door seal inspections, ensures that Pass Boxes remain in optimal working condition. Preventive maintenance reduces the likelihood of unexpected failures and extends the lifespan of critical components.
2. Rigorous Training Programs
Establishing rigorous training programs ensures that personnel adhere to SOPs and handle Pass Boxes correctly. Training focuses on proper door operations, maintenance procedures, and emergency responses, minimizing the risk of operator-induced deviations and enhancing overall contamination control.
3. Trending and Early Warning
Utilizing trending and early warning systems involves setting alert levels below action thresholds to detect potential issues before they escalate. Continuous monitoring and analysis of performance data enable timely interventions, preventing minor deviations from developing into major failures and ensuring sustained Pass Box performance.
IX. Documentation and Record-Keeping
A. GMP Documentation Principles
- Attributable: Every record must clearly identify who performed an action and when.
- Legible: Records should be easily readable and understandable.
- Contemporaneous: Documentation must be completed at the time the activity occurs.
- Original: Original records or certified copies must be maintained.
- Accurate: Information must be correct and reflect the true nature of the activity.
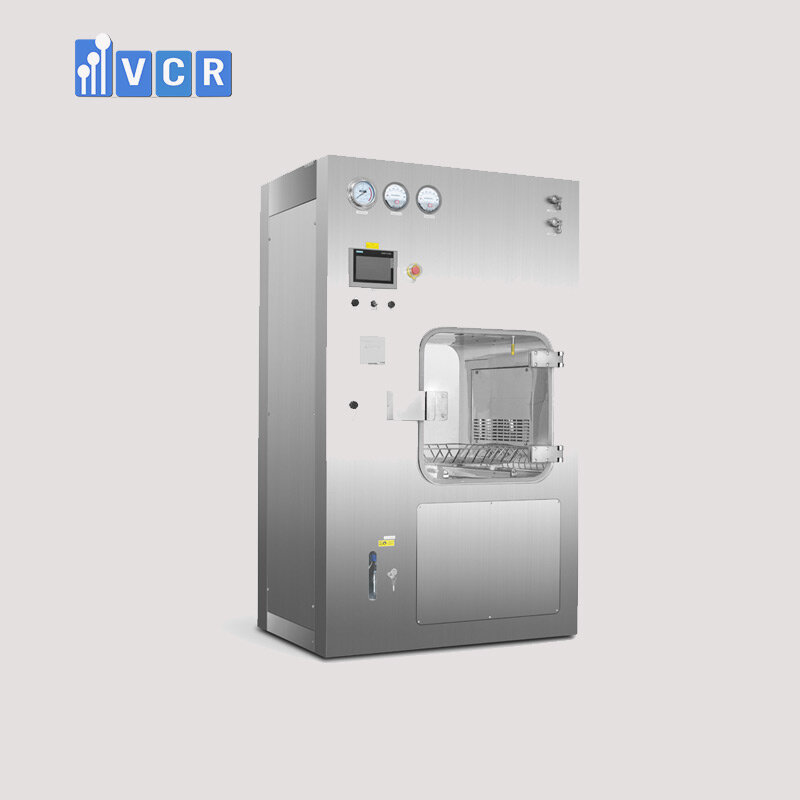
B. Types of Documentation in Pass Box Validation
C. Integration with Quality Management Systems (QMS)
D. Electronic Records and Data Management
E. Audit Trail Requirements
F. Ensuring Regulatory Compliance
X. Conclusion
A. Summary of Key Points
B. Best Practices and Future Trends
1. Risk-Based ValidationFinal Thoughts
PN