Installing reputable and quality cleanroom equipment - Choose VCR
Installing cleanroom equipment always requires meticulousness and care on each installation method, so sometimes it will encounter many difficulties. To find a reputable and quality clean room equipment installation unit, please find out with us through the article below.
To find a reputable and quality cleanroom equipment installation unit, please find out with VCR through the article below.
Cleanroom levels
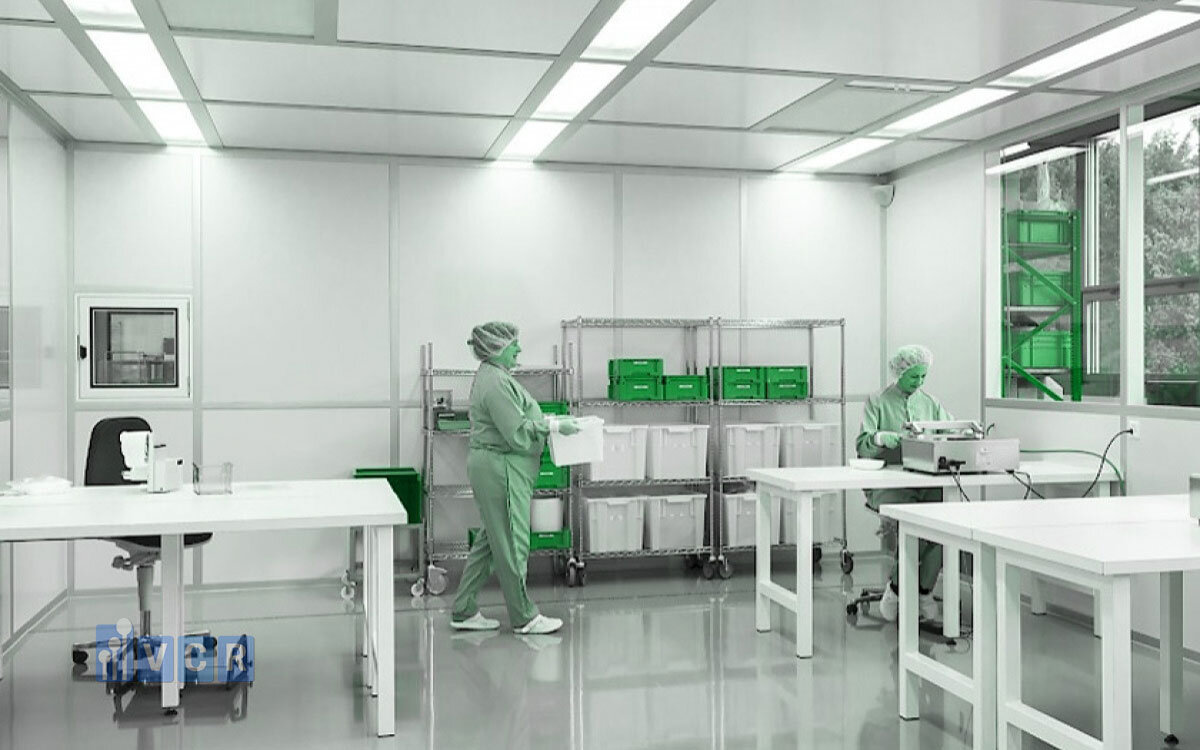
Classification according to ISO 14644-1
- ISO Class 1: This cleanroom has the highest cleanliness, only allowing very few dust particles in the air. Used in extremely demanding applications such as microchip production, nanotechnology.
- ISO Class 2 - 4: Used in fields that require high accuracy such as semiconductor manufacturing, optics, and microbiology.
- ISO Class 5: Equivalent to the Class 100 cleanroom level according to the old standard (Federal Standard 209E). Commonly used in the pharmaceutical industry and biotechnology laboratories.
- ISO Class 6 - 7: Used for industries such as manufacturing medical instruments, medical equipment or in safe food production processes.
- ISO Class 8 - 9: These are cleanrooms with lower requirements, often used in industries that do not require too much cleanliness such as the production of electronic components.
Read more: What Is ISO 8, ISO 7, ISO 6, ISO 5 Cleanroom?
Classified according to Federal Standard 209E (FED 209E)
- Class 1: This cleanroom only allows a maximum of 1 particle with a size of 0.5 um or larger in 1 cubic foot of air.
- Class 10: Up to 10 particles with a size of 0.5 um or larger in 1 cubic foot of air.
- Class 100 (equivalent to ISO 5): cleanrooms have a maximum of 100 0.5 um dust particles in 1 cubic foot of air. This type of cleanroom is popular in pharmaceuticals and biotechnology.
- Class 1000 (equivalent to ISO 6): This cleanroom is often used in light industries and manufacturing electrical components.
- Class 10000 (equivalent to ISO 7): Application in industries that require average cleanliness.
- Class 100000 (equivalent to ISO 8): Used in food production or assembly of precision mechanical products.
Classified by industry
- Pharmaceutical industry: cleanroom requirements at the level of ISO 5 to ISO 8, with the purpose of ensuring that there is no bacterial infection during the production of drugs, vaccines, and medical equipment.
- Microchip, semiconductor manufacturing industry: Often need a cleanroom ISO Class 1 to Class 5, because just a small piece of dust can damage products.
- Food and beverage industry: ISO Class 7 to Class 8, where hygiene control is needed to ensure the safety of consumers.
What should be paid attention to in the construction of a cleanroom?
Cleanroom standards and levels
Read more: Top frequently asked questions about cleanroom construction
Air control system
- HEPA or ULPA air filtration system: These are filters that must ensure the removal of almost all dust particles and bacteria in the air. Depending on the level of the cleanroom, the type of scale filter used may be different.
- Number of air exchangers (ACH): Must ensure that clean air flow is replaced regularly to maintain air quality inside the cleanroom. For high-level cleanrooms, airflow needs to be continuously circulated.
- Room pressure: Must control the positive pressure or negative pressure in the cleanroom depending on specific requirements, in order to avoid pollution from outside entering or vice versa.
Cleanroom construction materials
- Walls and ceilings: Usually made of composite or aluminum panels, dustproof and easy to clean.
- Cleanroom floor: The floor must be flat, easy to clean and dust-resistant. Vinyl, epoxy or polyurethane are popular choices.
- Doors and doors: Must be made of sealed materials, do not generate particles, and ensure complete isolation from the external environment.
Lighting system
- Lighting meets the standard for each industry, usually white light with enough brightness to work.
- Lamps do not generate heat or ultraviolet rays that can affect air quality or increase the room temperature.
HVAC system
- Temperature and humidity are maintained at an appropriate level, not only ensuring the working environment but also helping to maintain the operation of the air filtration system.
- Rotating airflow ensures no interruption and optimizes the ability to control dirt and bacteria.
Changing room and airlock
- Employees must change specialized clothes before entering the cleanroom to prevent contamination.
- Airlock between areas with different levels of cleanliness helps prevent air from the external environment from entering the cleanroom.
Control and monitoring system
Cleanroom maintenance and cleaning
- Surface cleaning: The surfaces in the cleanroom must be cleaned regularly with non-polluting solutions.
- Periodic filter replacement: HEPA/ULPA filters need to be replaced from time to time to ensure functionality.
- Periodic inspection: There must be a schedule for inspection and maintenance of HVAC systems, air filtration, and other systems.
Staff training
Vietnam Cleanroom Equipment - Reputable and quality cleanroom equipment installation unit
Why should you choose VCR as a cleanroom equipment installation unit?
Experience and expertise: VCR has many years of experience in the design and installation of cleanroom systems that meet international standards such as ISO 14644-1, GMP, FED 209E, and EU GMP. With a team of experienced engineers and extensive professional knowledge, we are committed to bringing the most optimal solutions to customers.
Comprehensive solution: We provide a package solution from consulting, equipment supply to system construction and maintenance. Customers can rest assured about all aspects of the cleanroom from HEPA air purification system, HVAC, pressure control system, to auxiliary equipment such as air shower, pass box, fume hood and lighting.
High quality products: All equipment and materials that VCR used meet international standards are thoroughly checked for quality. We import and distribute products from the world's leading brands to ensure durability, safety and high performance.
Install accurately and on schedule: VCR always carries out projects on schedule without affecting the quality of the work. Our construction team is well-trained, strictly following the cleanroom installation procedures to ensure an absolutely clean space immediately after completion
VCR fields of cleanroom construction
- Pharmaceutical and medical industry: We provide cleanroom solutions that meet GMP standards, suitable for the production of drugs, vaccines, and medical equipment. These cleanrooms ensure sterility and strict control of environmental factors.
- Electronics and semiconductor industry: cleanroom construction meets ISO Class 1 to Class 5 standards, ensuring no dirt contamination or impurities that can affect microchips and small components.
- Food and beverage industry: VCR provides cleanroom solutions to ensure food hygiene and safety during production, packaging, and storage.
Cleanroom construction process at VCR