An Overview of ISO 4 Cleanroom - Class 10 Cleanroom
An ISO 4 cleanroom is an ultra-clean controlled environment designed to meet strict standards.
- An Overview of ISO 4 Cleanroom - Class 10 Cleanroom
- ISO 4 Cleanroom Standard - Class 10 Cleanroom
- Technical Parameters to Consider When Designing an ISO 4 Cleanroom
- Equipment Required in an ISO 4 Cleanroom
- Notes on Gowning Room and Cleanroom Management
- Requirements for Testing and Maintenance of Class 10 Cleanroom
An Overview of ISO 4 Cleanroom - Class 10 Cleanroom
An ISO 4 cleanroom is an ultra-clean controlled environment designed to meet strict standards. It finds its primary application in nano-technology, semiconductor materials, and controlled zones within biotechnology and pharmaceutical processes, such as filling lines or other critical procedures.
According to the ISO 14644-1 standard, an ISO 4 cleanroom allows no more than 352 particles with a size ≥0.5μm per cubic meter. Following the STD 209E standard, an ISO 4 cleanroom is referred to as a Class 10 cleanroom, allowing a maximum of 10 particles with a size ≥0.5μm per cubic foot.
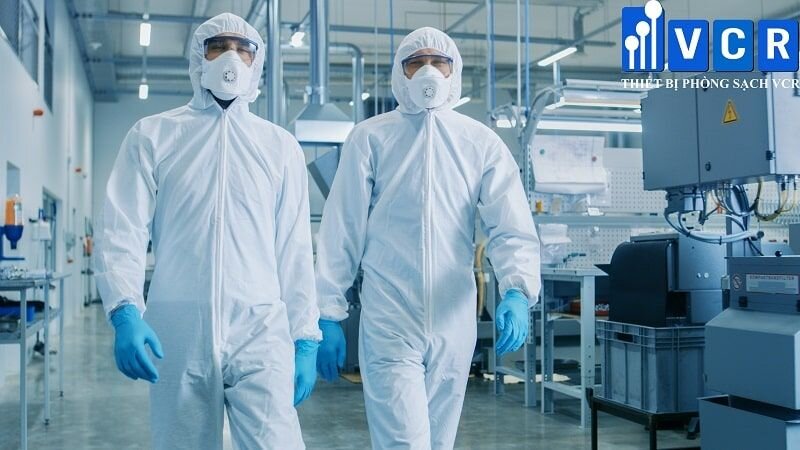
ISO 4 Cleanroom Standard - Class 10 Cleanroom
An ISO 4 cleanroom - as defined by the ISO 14644-1 standard, which measures particle count per cubic meter, is also referred to as a Class 10 cleanroom - according to the STD 209E standard, which measures particle count per cubic foot. Let's now delve into the particle levels of this cleanroom according to these two aforementioned standards:
ISO 4 Cleanroom Standard per ISO 14644-1
The ISO 14644-1 standard specifies the permissible particle count in a cubic meter of air. For an ISO 4 cleanroom, the particle count standards are as follows:
Size |
≥0.1 µm |
≥0.2 µm |
≥0.3 µm |
≥0.5 µm |
≥1 µm |
≥5 µm |
Particle count |
10.000 |
2.370 |
1.020 |
352 |
83 |
Class 10 Cleanroom Standard per STD 209E
The STD 209E standard indicates the permissible particle count in a cubic foot of air. For a Class 10 cleanroom, we have the following particle count standards:
Size |
≥0.1 µm |
≥0.2 µm |
≥0.3 µm |
≥0.5 µm |
≥1 µm |
≥5 µm |
Particle count |
350 |
75 |
30 |
10 |
Technical Parameters to Consider When Designing an ISO 4 Cleanroom
Below are a few technical parameters to consider when designing an ISO 4 cleanroom:
Filtration Control and Particle Size
- Emphasizing Control of Particles with Sizes Larger than 0.5µm and Smaller than 5.0µm
- The primary focus lies in controlling particles with sizes ranging from larger than 0.5µm to smaller than 5.0µm. Achieving an exceptionally high filtration efficiency is paramount, which is accomplished through the use of Ultra-Low Penetration Air (ULPA) filters, achieving a remarkable 99.9995% efficiency at 0.12µm.
- The terminal stage of the filtration process will utilize either a Hepa Box, a Fan Filter Unit, or a Plenum module, contingent upon the specific application of the cleanroom.
- A maximum of 352 particles with sizes ≥0.5µm per cubic meter of air is permissible. Correspondingly, a maximum of 10 particles with sizes ≥0.5µm per cubic foot of air is allowable.
- Environmental factors such as temperature, humidity, illumination levels, noise, vibration, static control, and exhaust will be meticulously tailored to each cleanroom's application within the design.
- High air velocity and frequent air changes are requisite for the cleanroom's operation. Employing exclusively ULPA filters ensures an exceptionally high filtration efficiency.
- The specifics of cleanroom design will ascertain the exact requirements for each environmental parameter, ensuring they align with the intended application of the cleanroom.
Airflow and Air Exchange Rate in ISO 4 Cleanroom
- Laminar Flow is a mandatory requirement in ISO 4 cleanroom
- The average air exchange rate typically falls within the range of 300 to 540 exchanges per hour.
- The filter efficiency coverage should ideally be between 90% to 100%.
Architectural Enhancements
Wall Structure
Similar to an ISO 4 cleanroom, the construction of walls follows a modular approach, adapted to the specific requirements of the cleanroom. For biotechnology applications, a stable design is essential, incorporating seamless connections and curved profiles to eliminate sharp 90-degree angles. This configuration facilitates wet cleaning and the application of vaporized hydrogen peroxide (VHP) misting to meet stringent aseptic criteria. Conversely, Nano technology and other non-aseptic cleanroom types require regular dry wiping or dust extraction.
Ceiling Structure
The ceiling design is purpose-built for ISO 4 cleanroom, tailored to the unique requirements of each cleanroom's application. For biotechnology and pharmaceutical applications, a typical modular ceiling system is often utilized to achieve adequate filter coverage and appropriate illumination levels.
Nano technology and other non-aseptic applications often employ grid systems with gasketed panels or flat grid systems for smaller rooms, incorporating either gasketed or integrated lighting panels.
Flooring Structure for Class 10 Cleanroom
Raised access flooring with perforated tiles is employed for nano technology applications. In biotechnology and pharmaceutical contexts, a vinyl flooring system is commonly utilized, primarily in surrounding areas such as RABs (Restricted Access Barrier Systems) or downflow zones. Each system may feature diverse attributes, including chemical resistance, coving, static control, load-bearing capacity, and slip resistance.
Other architectural features encompass various entry types, observation windows, glass partitions, pass-throughs, water sprinklers/fire prevention mechanisms, Wi-Fi/network access, security cameras, and access control devices.
Air return grilles: Low-wall or raised access floor configurations are used to facilitate air circulation and return.
Equipment Required in an ISO 4 Cleanroom
An ISO 4 cleanroom demands a stringent level of cleanliness (even more so than an ISO 5 cleanroom), necessitating specific equipment to meet its standards.
The following are essential equipment for an ISO 4 cleanroom:
- Dynamic Pass Box
- Fan Filter Unit
- Air Shower
- Airlock
- Air Handling Unit (AHU)
- Cleanroom Lighting
- Laminar Air Flow Unit
- BIBO
Depending on the cleanroom's application, additional equipment might be necessary, such as Dispensing Booths, Isolator Cabinets, Decontamination Chambers, Laminar Air Flow Trolleys, and more.
Other accessories and requirements that a Class 10 cleanroom should have include:
- Cleanroom Gowning
- Sticky Mats
- Vinyl Flooring or Self-Leveling Epoxy Coated Floor
- Cleanroom Supplies
- Cleanroom Stainless Steel Furnitures
Notes on Gowning Room and Cleanroom Management
Clothing Requirements: Full attire, including head cover, beard cover, shoe covers, often with a face shield and exhalation filter for employees, as well as gloves suitable for the task (such as vinyl, rubber, nitrile).
Airlock Area: Isolated (typically at a lower pressure and with less strict classification, often an ISO 5 Air Lock) prior to entering the ISO 4 cleanroom or designated zone.
Prohibited Use of Particle-Generating Materials: The use of particle-generating materials such as used paper, hardboard, pallets, and dry erase boards is not allowed.
Requirements for Testing and Maintenance of Class 10 Cleanroom
- Particle Count Verification: Maximum interval of 6 months, following ISO 14644-1 Appendix A testing procedures.
- Pressure Differential Check: Maximum interval of 6 months, in accordance with ISO 14644-1 Appendix B5 testing procedures.
- Airflow Velocity Examination: Maximum interval of 6 months, as per ISO 14644-1 Appendix B4 testing procedures.
PN