FMEA là gì ? Cách phân tích sai hỏng và những tác động của nó tới doanh nghiệp
Hiện nay, FMEA đang được ứng dung ngày một phổ biến, hứa hẹn mang lại nhiều lợi ích cho các tổ chức, doanh nghiệp bởi khả năng phòng ngừa và nhận diện mọi rủi ro.
- 1. FMEA là gì?
- 2. FMEA được áp dụng khi nào ?
- 3. Phân loại FMEA trong sản xuất
- 4. Lý do thực hiện phân tích lỗi và ảnh hưởng của FMEA
- 5. Các bước thực hiện phân tích FMEA
- Bước 1: Chuẩn bị
- Bước 2: Xếp hạng theo mức độ nghiêm trọng
- Bước 3: Xác định được những nguyên nhân tiềm tàng
- Bước 4: Liệt kê hết các kiểu sai lỗi có thể xuất hiện trong mỗi chức năng
- Bước 5: Phân công thực hiện
- Bước 6: Đánh giá khả năng phát hiện sai lỗi
- Bước 7: Xếp hạng hệ số rủi ro RPN, kết thúc chu trình
- 6. Mối quan hệ giữa FMEA với việc giải quyết vấn đề
- 7. Ưu điểm và nhược điểm của FMEA
Vậy FMEA là gì ? cách nó thực hiện phân tích sai hỏng và lỗi như thế nào & Cách nó áp dụng trong IATF 16949 ra sao ?
Cùng Thiết bị phòng sạch VCR tìm hiểu qua bài viết dưới đây nhé !
1. FMEA là gì?
FMEA là viết tắt của cụm từ Failure Mode Effects Analysis, đây là một phương pháp phân tích dạng lỗi và những tác động tới đầu ra hay là thành phẩm của quy trình. Cụ thể như sau:
- Failure (Sự sai hỏng): trong FMEA, sự sai hỏng được nhấn mạnh là các lỗi tiềm ẩn có thể xảy ra trong tương lai, chứ không phải lỗi đã xảy ra.
- Mode (Cách thức): trong FMEA nó có ý nghĩa là phương thức, nguyên nhân gây ra sai hỏng. Tránh nhầm lẫn 2 khái niệm Failure Mode (cơ chế, nguyên nhân) và Defect (thiên về phân loại phế phẩm).
- Effect ( Ảnh hưởng, tác động): là sự ảnh hưởng của những lỗi sai, hậu quả như thế nào, tác động ra sao đến thành phẩm (đầu ra) của quá trình. Ví dụ: Sản phẩm có vết trầy xước trên bán thành phẩm thì chỉ là lỗi ngoại quan, nhưng nó xảy ra trên bao bì sản phẩm có thể dẫn đến hư hại sản phẩm bên trong.
- Analysis (Phân tích): nghĩa là phải tìm hiểu nguyên nhân, phân tích lỗi sai, những rủi ro và hậu quả, từ đó đưa ra hướng cải tiến thích hợp.
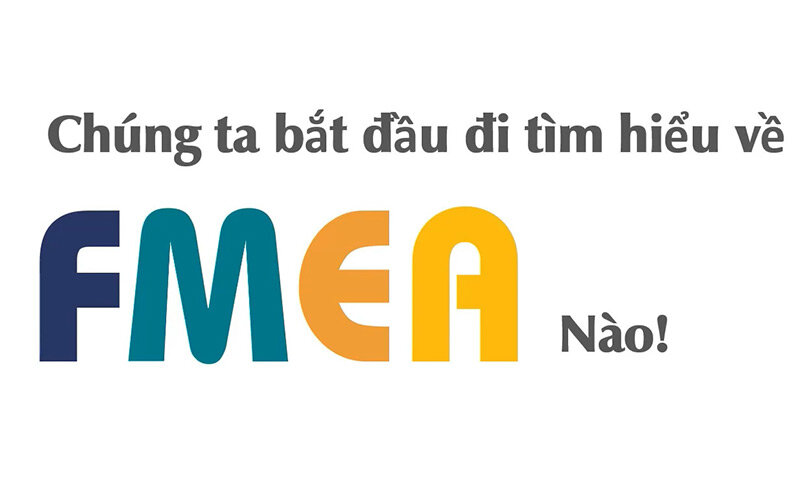
Là một trong những phương pháp có cấu trúc cao, FMEA có hệ thống đầu tiên phân tích lỗi xảy ra trong quá trình thiết kế, sản xuất và là một trong những công cụ cốt lõi của IATF 16949. Nó còn có tên gọi khác là phân tích ảnh hưởng của chế độ lỗi tiềm ẩn, chế độ hoặc hiệu ứng và mức độ nghiêm trọng của lỗi phân tích.
Đây cũng là một công cụ được áp dụng nhằm đảm bảo những vấn đề tiềm ẩn được xem xét, giải quyết trong suốt quy trình nào đó. Từ đó có thể đề xuất các biện pháp, hạn chế tối đa những rủi ro không lặp lại nữa.
2. FMEA được áp dụng khi nào ?
Một số trường hợp như sau cần áp dụng FMEA:
- Trường hợp một quy trình, dịch vụ hay sản phẩm đang được thiết kế hay thiết kế lại, sau khi triển khai chức năng chất lượng (QFD)
- Khi quy trình, dịch vụ, sản phẩm đang hiện có và áp dụng theo một cách mới.
- Trước khi phát triển kế hoạch kiểm soát cho quy trình mới hoặc sửa đổi.
- Trường hợp các mục tiêu cải tiến được lên kế hoạch cho một quy trình, dịch vụ hoặc sản phẩm hiện có.
- Trường hợp phân tích lỗi trong một quy trình, dịch vụ hoặc sản phẩm hiện có
- Định kỳ suốt vòng đời quy trình, sản phẩm hay dịch vụ.
3. Phân loại FMEA trong sản xuất
FMEA có 2 dạng như sau:
3.1. FMEA thiết kế - Design FMEA, FMEA-D hoặc D-FMEA
Dạng này chú trọng chủ yếu đến việc tối ưu hóa độ khả thi sản phẩm. Mục đích của nó là đảm bảo tất cả những sai lỗi tiềm ẩn và nguyên nhân hình thành được nhận định và nghiên cứu. Nhằm đánh giá khách quan công tác thiết kế sản phẩm, doanh nghiệp cần nghiên cứu những thông số sản phẩm dưới đây:
- Thuộc tính
- Hình dáng bên ngoài;
- Dung sai và Giao diện;
- Tương tác hệ thống;
- Hồ sơ của người dùng
3.2. FMEA quy trình - Process FMEA, FMEA-P hoặc P-FMEA
Với dạng này nó chú trọng chủ yếu tới việc cải thiện năng suất đến từ các phương tiện sản xuất như máy móc, dây chuyền sản xuất,… và chuỗi cách thức, tiếp đón khách hàng, truy cập thông tin,… mà doanh nghiệp đang sử dụng. Nhằm nhận định các cách thức sinh ra những sai sót tiềm ẩn cho sản phẩm và quy trình sản xuất, doanh nghiệp cần nghiên cứu một số chỉ tiêu dưới đây.
- Phương pháp đang ứng dụng, hệ thống đo lường
- Vật liệu, máy móc
- Yếu tố con người và yếu tố hiệu suất
4. Lý do thực hiện phân tích lỗi và ảnh hưởng của FMEA
Trong sản xuất, việc phát hiện hàng lỗi càng sớm thì những ảnh hưởng nó gây ra càng nhỏ và ngược lại khi lỗi phát hiện quá muộn thì những tác động của nó sẽ rất lớn, từ việc chi phí sản xuất gia tăng tới những khoản bồi thường cực kỳ lớn vì không cam kết chất lượng, nghiêm trọng hơn là uy tín của doanh nghiệp sẽ bị giảm đi rất nhiều.
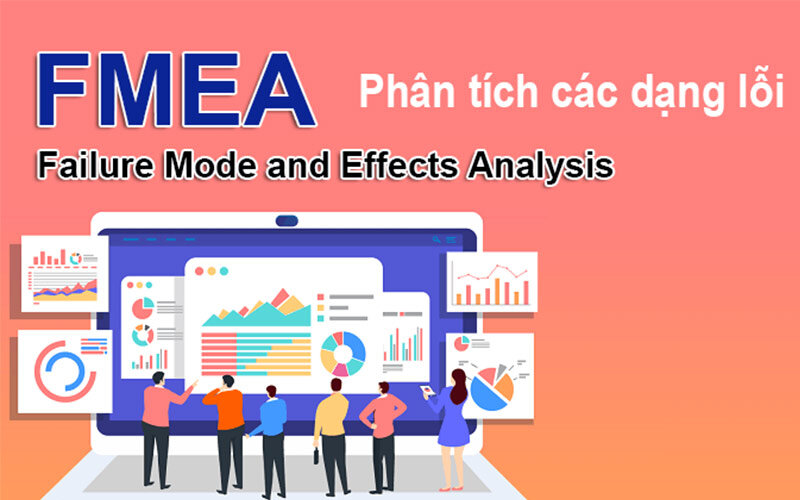
FMEA là một trong các công cụ ngoài việc cho phép phát hiện lỗi còn giúp ngăn ngừa tác động hư hỏng một cách cơ bản. Bằng cách dùng công cụ FMEA để phát hiện lỗi trong quá trình sản xuất với thời gian sớm nhất sẽ mang lại một số lợi ích sau cho doanh nghiệp:
- Xác định điểm hay khu vực thực sự cần cải tiến trong sản phẩm, quá trình. Điều này, giúp cho công ty tối ưu thời gian và chi phí.
- Theo dõi các sai sót tiềm ẩn trong quá trình thiết kế
- Phòng ngừa, ngăn chặn những thất bại có thể xảy ra trong sản phẩm hay trong các quá trình hoạt động của tổ chức, doanh nghiệp.
- Cải thiện những chức năng có trong sản phẩm.
5. Các bước thực hiện phân tích FMEA
Bước 1: Chuẩn bị
Trước khi thực hiện FMEA, tất cả yêu cầu kỹ thuật cho sản phẩm, quy trình và phạm vi của FMEA cần được thu thập, xem xét kỹ lưỡng. Điều này để đảm bảo doanh nghiệp có đủ thông tin cần thiết cho quá trình thực hiện FMEA. Các tài liệu gồm có:
- Giả định về thiết kế hoặc quy trình;
- Hóa đơn sơ bộ về thành phần hoặc vật liệu;
- Các nguyên nhân tiềm ẩn từ những giao diện khác nhau;
- Nguyên nhân tiềm tàng từ lựa chọn thiết kế;
- Nguyên nhân tiềm tàng từ môi trường và tiếng ồn;
- Những phương pháp kiểm tra, thử nghiệm trước đây được dùng trên những sản phẩm tương tự…
Bước 2: Xếp hạng theo mức độ nghiêm trọng
Ở khâu quản lý chất lượng bao gồm làm rõ các chức năng, chế độ lỗi, những ảnh hưởng của lỗi, xếp hạng theo mức độ nghiêm trọng. Những dữ liệu của doanh nghiệp cần quan tâm, gồm có:
- Thông số kỹ thuật thiết kế
- Quy định của chính phủ
- Những yêu cầu của chương trình
- Đặc điểm những sản phẩm cần phải phân tích
- Kết quả mong muốn ở quy trình
- Doanh nghiệp dự kiến giải pháp để thực hiện
Bước 3: Xác định được những nguyên nhân tiềm tàng
Nguyên nhân lỗi trong quá khứ, được doanh nghiệp xem xét cẩn trọng cùng các thông tin sau:
- Những biện pháp kiểm soát và phòng ngừa ở hiện tại
- Xếp hạng theo mức độ xuất hiện từng lỗi
- Giải pháp đã đưa ra nhằm xử lý lỗi nêu trên
- Việc tái phạm lỗi xuất hiện thường xuyên không?
Bước 4: Liệt kê hết các kiểu sai lỗi có thể xuất hiện trong mỗi chức năng
Kiểu sai lỗi là các tình huống xảy ra ở sản phẩm hay trong các quá trình, chúng không phù hợp với nhu cầu, mong muốn của khách hàng và nội bộ công ty, làm cho sản phẩm, quá trình đó không đáp ứng được yêu cầu. Ở giai đoạn này, thành viên trong FMEA sẽ cùng nhau tìm ra những sai lỗi tiềm ẩn trong từng khâu của tổ chức.
Bước 5: Phân công thực hiện
Doanh nghiệp xếp hạng theo mức độ nghiêm trọng, mức độ xuất hiện, mức độ phát hiện cho mỗi kết hợp lỗi/tác động tiềm ẩn, những nguyên nhân, cách kiểm soát. Sau đó tiến hành chỉ định thực hiện và ngày hết hạn hành động tới nhân viên.
Bước 6: Đánh giá khả năng phát hiện sai lỗi
FMEA sẽ kết thúc khi những biện pháp đối phó đã thực hiện thành công trong việc giảm thiểu những rủi ro. Nếu FMEA không phát hiện ra các rủi ro thì nó được xem là yếu kém, hoạt động quản lý chất lượng của doanh nghiệp đang thực hiện không có giá trị gia tăng. Việc đánh giá sẽ thực hiện độc lập giữa các thành viên.
Bước 7: Xếp hạng hệ số rủi ro RPN, kết thúc chu trình
Sau khi xác nhận đã hoàn thành bước 6, Giám đốc dự án hoặc trưởng nhóm thực hiện FMEA sẽ xác định theo mức độ nghiêm trọng, mức độ xuất hiện, mức độ phát hiện rồi so sánh với RPN đã sửa đổi, cải tiến đối với thiết kế hay quy trình được ghi nhận trong hệ thống quản lý chất lượng của doanh nghiệp.
6. Mối quan hệ giữa FMEA với việc giải quyết vấn đề
Chắc chắn những lỗi được phát hiện trong quy trình FMEA sẽ gây ra những ảnh hưởng không hề nhỏ cho doanh nghiệp nếu như không điều chỉnh kịp thời. Nguyên nhân lỗi được phát hiện từ FMEA tương đương với các nguyên nhân gốc rễ, tiềm ẩn mà doanh nghiệp bắt buộc phải thừa nhận và phải giải quyết vấn đề.
Ngoài ra, để lập kế hoạch tương lai cho tổ chức, các dữ liệu thu thập từ việc giải quyết vấn đề sẽ đưa vào quy trình FMEA. Điều này sẽ cho phép FMEA xem xét những hư hỏng thực tế, khả năng phân loại chế độ, các nguyên nhân hỏng. Từ đó, việc giải quyết vấn đề sẽ hoạt động hiệu quả, hoàn thiện hơn.
7. Ưu điểm và nhược điểm của FMEA
Ưu điểm
- FMEA đang được ứng dụng phổ biến, rộng rãi cho những chế độ lỗi của thiết bị, hệ thống, con người cũng như phần mềm, phần cứng, quy trình,…
- Nó giúp tránh những sửa đổi thiết bị đắt đỏ bằng cách xác định những vấn đề trong khâu thiết kế, xác định điểm duy nhất của chế độ lỗi, những yêu cầu đối với hệ thống dự phòng hoặc an toàn.
- Bên cạnh đó, nó còn cung cấp đầu vào cho những chương trình giám sát phát triển bằng cách làm nổi bật tính năng chính cần giám sát.
Nhược điểm
- Nó chỉ được sử dụng để xác định những dạng hỏng đơn lẻ, không phải dạng hỏng hóc kết hợp. Trừ khi kiểm soát và tập trung hoàn toàn , các nghiên cứu tốn thời gian và chi phí.
- Với hệ thống phức tạp, nhiều lớp,… nó sẽ khó phát huy được những tác dụng của mình.
Trên đây là những nội dung của FMEA. Hi vọng qua bài viết sẽ giúp bạn có được những thông tin hữu ích.
Phuong.